Lean and Mean: The Impact of Lean Manufacturing Techniques on System Integration
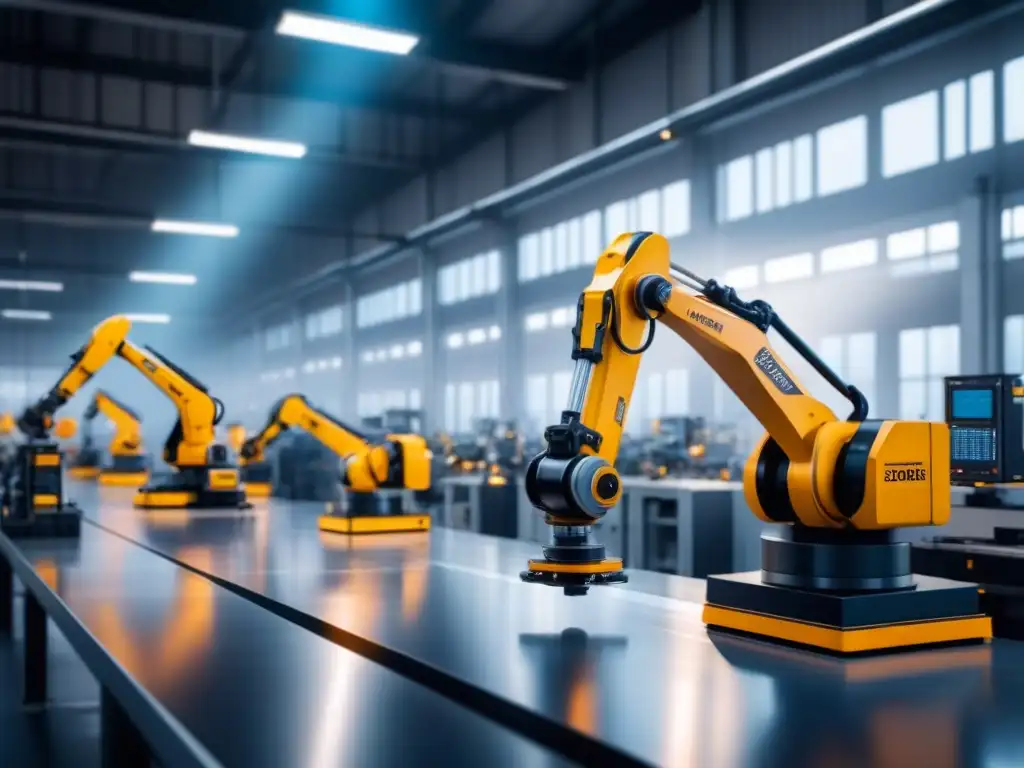
¡Bienvenido a Innovación Industrial, donde la vanguardia se encuentra con la manufactura! Sumérgete en el fascinante mundo de la integración de sistemas con nuestro artículo principal: "Lean and Mean: The Impact of Lean Manufacturing Techniques on System Integration". Descubre cómo las técnicas de Lean Manufacturing están transformando la forma en que las industrias se integran, ¡prepárate para un viaje de conocimiento e innovación sin límites!
- Introducción al Lean Manufacturing y su Influencia en la Integración de Sistemas
- Explorando el Impacto de las Técnicas Lean en la Integración de Sistemas
- Casos de Éxito: Empresas que Transformaron su Integración de Sistemas con Lean Manufacturing
- Herramientas y Técnicas Específicas de Lean para Mejorar la Integración de Sistemas
- Los Desafíos de Integrar Lean Manufacturing en la Infraestructura Actual
- Perspectivas Futuras: La Evolución de Lean Manufacturing y su Rol en la Integración de Sistemas
- Conclusión: Maximizando el Potencial de Lean Manufacturing para una Integración de Sistemas Efectiva
-
Preguntas frecuentes
- 1. ¿Qué es Lean Manufacturing y por qué es importante en la integración de sistemas?
- 2. ¿Cuál es el impacto de las técnicas de Lean Manufacturing en la productividad de una empresa?
- 3. ¿Cómo pueden las empresas implementar con éxito Lean Manufacturing en sus operaciones?
- 4. ¿Qué beneficios puede obtener una empresa al integrar Lean Manufacturing en sus sistemas?
- 5. ¿Cuál es el rol de la tecnología en la aplicación de Lean Manufacturing en la integración de sistemas?
- Reflexión final: El Impacto Duradero de las Técnicas de Lean Manufacturing en la Integración de Sistemas
Introducción al Lean Manufacturing y su Influencia en la Integración de Sistemas
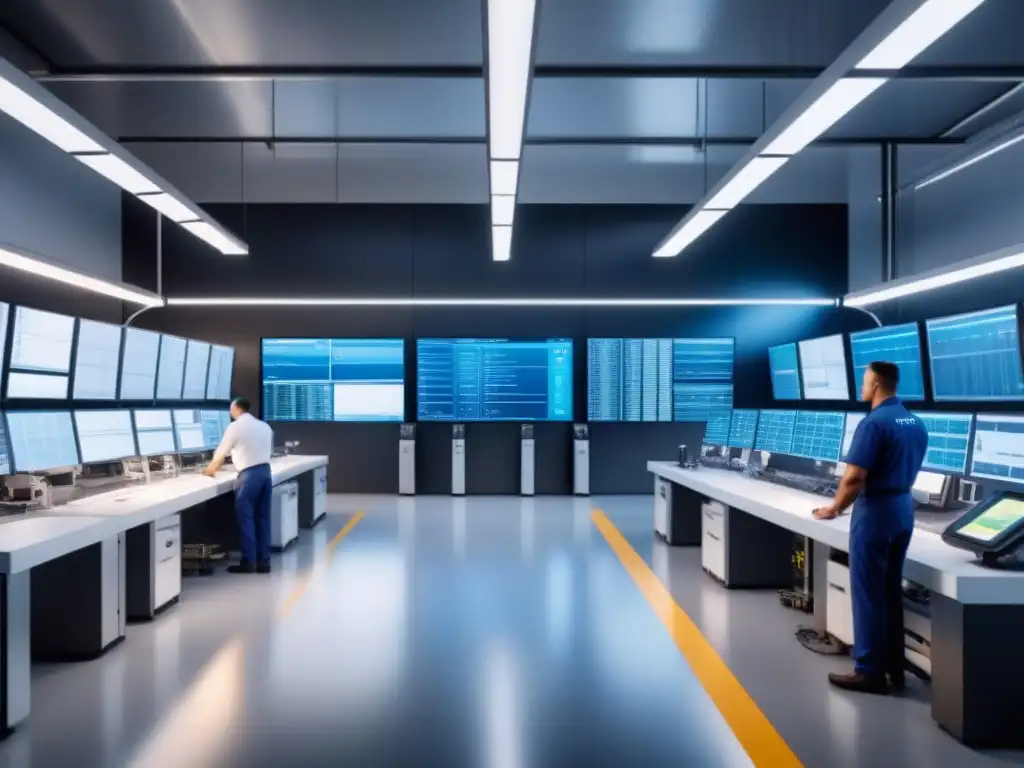
Definición y Principios Básicos del Lean Manufacturing
El Lean Manufacturing, también conocido como Manufactura Esbelta, es una filosofía de gestión que se centra en la eliminación de desperdicios en los procesos productivos para maximizar el valor para el cliente. Sus principios básicos incluyen la identificación y eliminación de actividades que no agregan valor, la optimización del flujo de trabajo, la mejora continua y el respeto por las personas.
Algunas de las herramientas más comunes utilizadas en el Lean Manufacturing son el Just-in-Time (JIT), el Sistema de Producción Toyota (TPS), el Kanban, la estandarización de procesos y la resolución de problemas mediante el método PDCA (Planificar, Hacer, Verificar, Actuar).
La implementación efectiva de los principios del Lean Manufacturing no solo reduce costos y tiempos de producción, sino que también fomenta la eficiencia, la calidad y la flexibilidad en la operación de las empresas.
La Evolución de las Técnicas Lean en la Industria Moderna
Con el avance de la tecnología y la digitalización de los procesos industriales, las técnicas Lean han evolucionado para adaptarse a las demandas cambiantes de la industria moderna. La integración de sistemas y la automatización han permitido una mayor eficiencia en la implementación de los principios Lean en las fábricas y plantas de producción.
La Industria 4.0 ha impulsado la convergencia entre la manufactura y la tecnología, facilitando la adopción de metodologías Lean en entornos altamente digitales. La conectividad de los sistemas, el uso de datos en tiempo real y la inteligencia artificial han potenciado la optimización de procesos y la toma de decisiones basadas en información precisa.
En la actualidad, las empresas que buscan mejorar su competitividad y eficiencia recurren a la integración de sistemas basados en los principios Lean para lograr una producción ágil, personalizada y sostenible en un mercado cada vez más dinámico y exigente.
Explorando el Impacto de las Técnicas Lean en la Integración de Sistemas
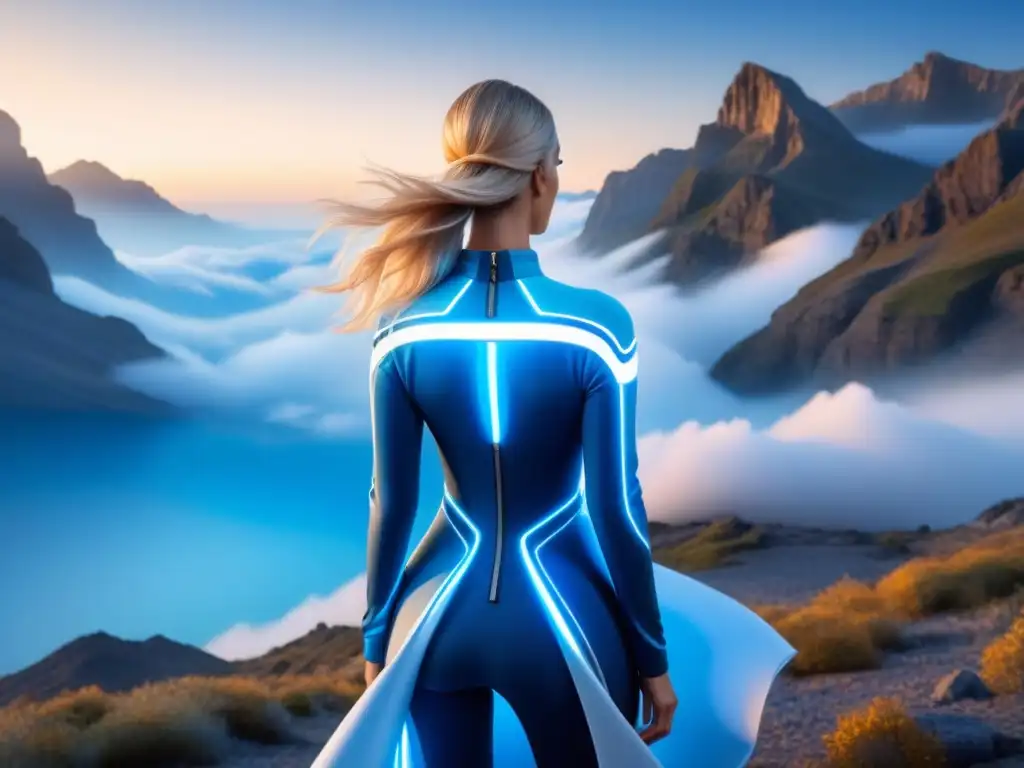
En el ámbito de la manufactura, la implementación de técnicas Lean ha demostrado tener un impacto significativo en la eficiencia operativa y la integración de sistemas. A través de la adopción de prácticas orientadas a la eliminación de desperdicios y la optimización de procesos, las empresas pueden mejorar su competitividad y su capacidad para adaptarse a un entorno cambiante.
La Lean Manufacturing se centra en la maximización del valor para el cliente al tiempo que minimiza el desperdicio de recursos. Al aplicar principios como la mejora continua, la estandarización de procesos y el trabajo en equipo, las organizaciones pueden lograr una mayor eficiencia operativa y una integración más fluida de sistemas en toda la cadena de valor.
La implementación de técnicas Lean en la manufactura no solo se traduce en una optimización de los procesos internos, sino que también facilita la integración de sistemas y la colaboración entre diferentes áreas de la empresa. Esto permite una mayor sincronización de actividades y una respuesta más ágil a las demandas del mercado.
Mejora de la Eficiencia Operativa a través de la Lean Manufacturing
La Lean Manufacturing se enfoca en identificar y eliminar actividades que no agregan valor al producto final, lo que se traduce en una mejora significativa de la eficiencia operativa. Al reducir los tiempos de producción, minimizar los tiempos de espera y optimizar el uso de recursos, las empresas pueden aumentar su capacidad de producción y responder de manera más efectiva a la demanda del mercado.
Además, la Lean Manufacturing fomenta una cultura de mejora continua en la organización, donde se promueve la participación activa de los empleados en la identificación de oportunidades de optimización y la implementación de soluciones efectivas. Esto no solo impulsa la eficiencia operativa, sino que también fortalece el compromiso y la motivación de los equipos de trabajo.
La implementación de técnicas Lean en la manufactura no solo conduce a una mayor eficiencia operativa, sino que también sienta las bases para una integración más efectiva de sistemas y procesos en toda la empresa.
Reducción de Costos y Aumento de la Calidad: Beneficios Clave
Uno de los principales beneficios de la Lean Manufacturing es la reducción de costos operativos a través de la eliminación de desperdicios y la optimización de procesos.
Al identificar y eliminar actividades innecesarias, las empresas pueden reducir sus gastos operativos y mejorar su rentabilidad.
Además, la Lean Manufacturing se asocia con un aumento en la calidad de los productos y servicios ofrecidos.
Al centrarse en la satisfacción del cliente y en la entrega de productos libres de defectos, las organizaciones pueden mejorar su reputación y fidelizar a sus clientes.
La implementación de técnicas Lean en la manufactura no solo conlleva una reducción de costos operativos, sino que también se traduce en un aumento de la calidad de los productos y servicios, lo que a su vez contribuye a fortalecer la posición competitiva de la empresa en el mercado.
Casos de Éxito: Empresas que Transformaron su Integración de Sistemas con Lean Manufacturing
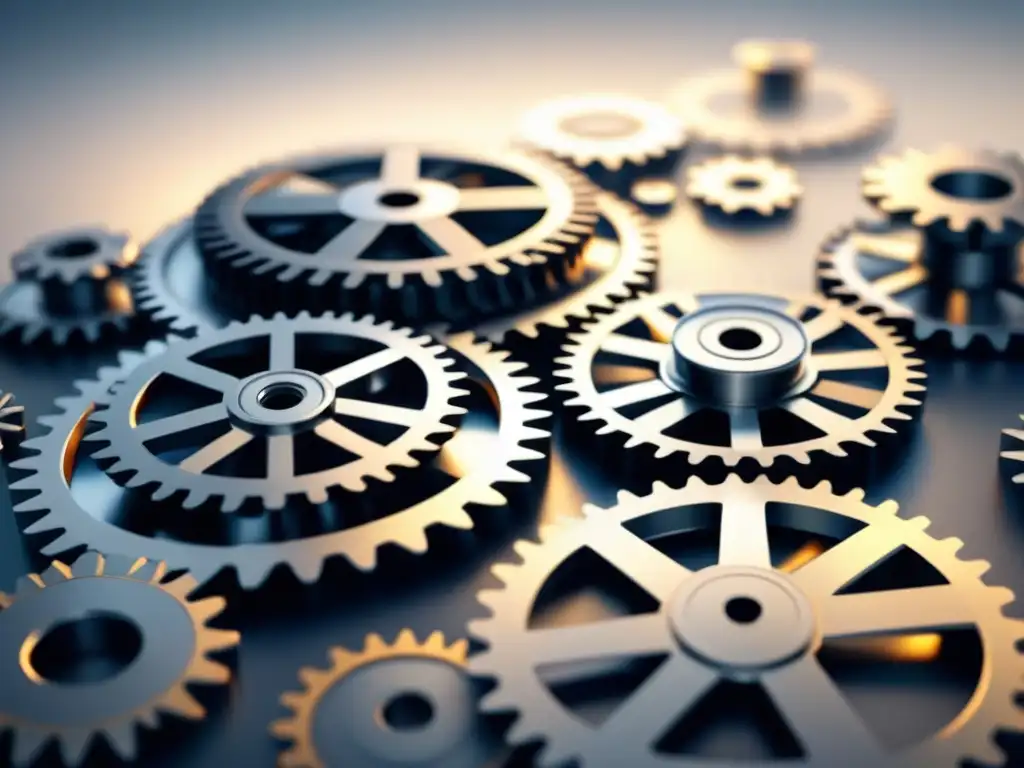
El Caso de Toyota: Pioneros en la Aplicación del Lean Manufacturing
Toyota Motor Corporation es reconocida a nivel mundial por ser pionera en la implementación exitosa del Lean Manufacturing en su proceso de producción. Esta metodología, también conocida como Sistema de Producción Toyota, se ha convertido en un referente en la industria automotriz y ha sido adoptada por numerosas empresas en diferentes sectores.
El enfoque de Toyota se basa en la eliminación de desperdicios, la mejora continua y la optimización de procesos para lograr una mayor eficiencia y calidad en la producción. Gracias a la aplicación del Lean Manufacturing, Toyota ha logrado reducir los tiempos de producción, disminuir los costos operativos y mejorar la satisfacción del cliente.
Uno de los pilares fundamentales del éxito de Toyota radica en la involucración de todos los niveles de la organización en la implementación de prácticas lean, fomentando la colaboración, la innovación y el aprendizaje continuo.
Innovaciones en Lean Manufacturing: El Ejemplo de General Electric
General Electric (GE) es otra empresa que ha destacado por su enfoque innovador en la aplicación de Lean Manufacturing. A través de su programa "GE Work-Out", la compañía ha logrado transformar sus procesos de producción y mejorar significativamente su eficiencia operativa.
GE ha integrado con éxito las prácticas lean en todas sus operaciones, desde la fabricación hasta la logística, permitiéndole reducir costos, mejorar la calidad de sus productos y aumentar la velocidad de entrega a los clientes. Esta implementación ha sido clave para la competitividad y el crecimiento sostenible de la empresa en un mercado global cada vez más exigente.
La cultura de mejora continua y la capacidad de adaptación de GE han sido fundamentales para el éxito de su estrategia de Lean Manufacturing, demostrando que la innovación y la eficiencia pueden ir de la mano para impulsar la excelencia operativa.
Herramientas y Técnicas Específicas de Lean para Mejorar la Integración de Sistemas

El Uso de la Metodología Kaizen para la Mejora Continua
La metodología Kaizen, originaria de Japón, se ha convertido en un pilar fundamental en el mundo de la manufactura gracias a su enfoque en la mejora continua. En el contexto de la integración de sistemas, la aplicación de Kaizen implica la identificación constante de áreas de mejora, la implementación de soluciones prácticas y la evaluación periódica de los resultados obtenidos. Esta filosofía fomenta la colaboración entre los distintos equipos de trabajo, promoviendo la eficiencia y la calidad en los procesos de integración.
Al incorporar la metodología Kaizen en el entorno de la manufactura, las empresas pueden optimizar la integración de sistemas al enfocarse en la eliminación de desperdicios, la estandarización de procesos y la búsqueda constante de la excelencia operativa. Esto no solo impacta positivamente en la eficiencia de la producción, sino que también contribuye a la mejora de la calidad, la reducción de costos y la satisfacción del cliente.
Mediante la implementación de Kaizen, las organizaciones pueden adaptarse de manera proactiva a los cambios del mercado, identificar oportunidades de innovación y fortalecer su posición competitiva en un entorno empresarial cada vez más dinámico y exigente.
Implementación de Sistemas Kanban para una Producción Eficiente
Los sistemas Kanban, inspirados en el modelo de producción de Toyota, se han consolidado como una herramienta poderosa para optimizar la gestión de inventarios, la planificación de la producción y la sincronización de los procesos en el entorno manufacturero. En el contexto de la integración de sistemas, la implementación de sistemas Kanban permite visualizar de manera clara y sencilla el flujo de trabajo, identificar cuellos de botella y garantizar una producción eficiente y sin interrupciones.
Al utilizar sistemas Kanban en el proceso de integración de sistemas, las empresas pueden coordinar de manera efectiva las actividades de diferentes departamentos, mejorar la comunicación entre equipos multidisciplinarios y reducir los tiempos de espera. Esta herramienta facilita la identificación de prioridades, la asignación eficiente de recursos y la adaptación ágil a los cambios en la demanda del mercado, contribuyendo a una integración de sistemas fluida y eficaz.
La implementación de sistemas Kanban no solo promueve la eficiencia operativa, sino que también impulsa la colaboración entre los equipos de trabajo, la transparencia en los procesos y la toma de decisiones basadas en datos concretos. Esto se traduce en una mayor flexibilidad, una reducción de los tiempos de producción y una mejora significativa en la calidad de los productos y servicios ofrecidos.
Los Desafíos de Integrar Lean Manufacturing en la Infraestructura Actual
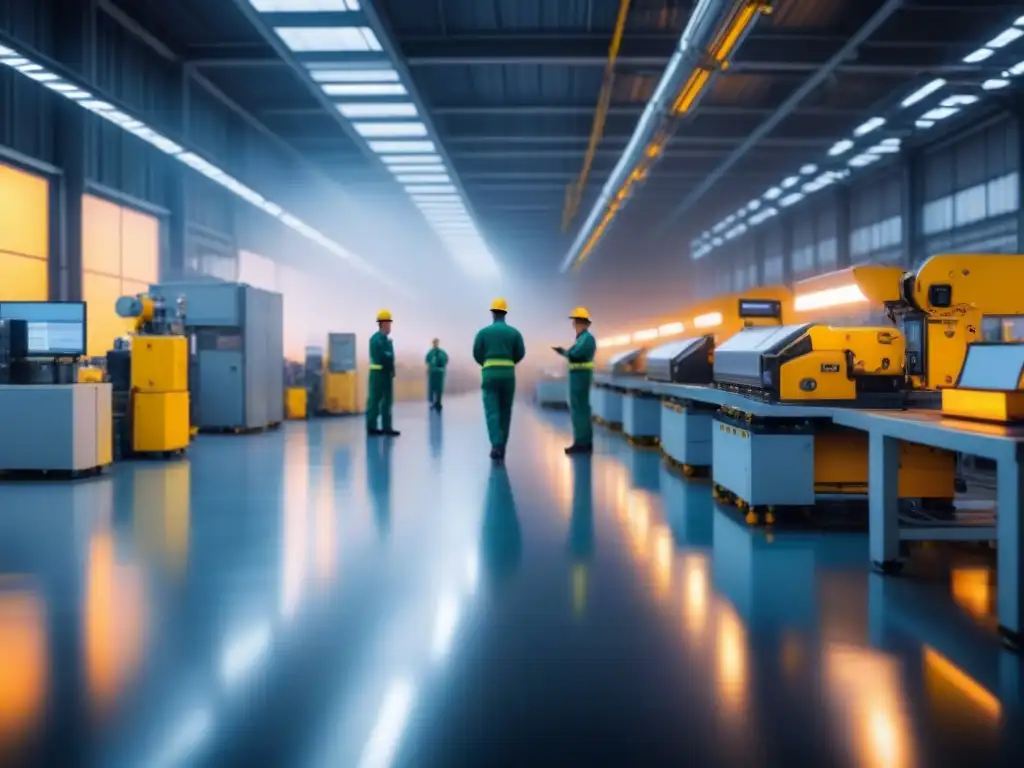
La implementación de técnicas de Lean Manufacturing en un entorno empresarial puede presentar desafíos significativos, especialmente cuando se trata de integrar estas prácticas en la infraestructura existente. Uno de los principales obstáculos a los que se enfrentan las organizaciones es superar las barreras culturales y organizacionales que pueden obstaculizar la adopción exitosa de Lean Manufacturing.
Las empresas a menudo se encuentran con resistencia al cambio por parte de los empleados que están acostumbrados a métodos de trabajo tradicionales. Para superar esta barrera, es fundamental establecer una cultura organizacional que fomente la innovación, la colaboración y la mejora continua. La comunicación efectiva y la participación activa de los empleados en el proceso de implementación son clave para garantizar el éxito de la integración de Lean Manufacturing.
Además, la estructura organizativa existente puede no ser compatible con los principios de Lean Manufacturing, lo que puede dificultar la implementación efectiva de estas técnicas. Es fundamental identificar y eliminar las prácticas y procesos obsoletos que no agregan valor, y reorganizar la estructura organizativa para optimizar la eficiencia y la productividad.
Perspectivas Futuras: La Evolución de Lean Manufacturing y su Rol en la Integración de Sistemas
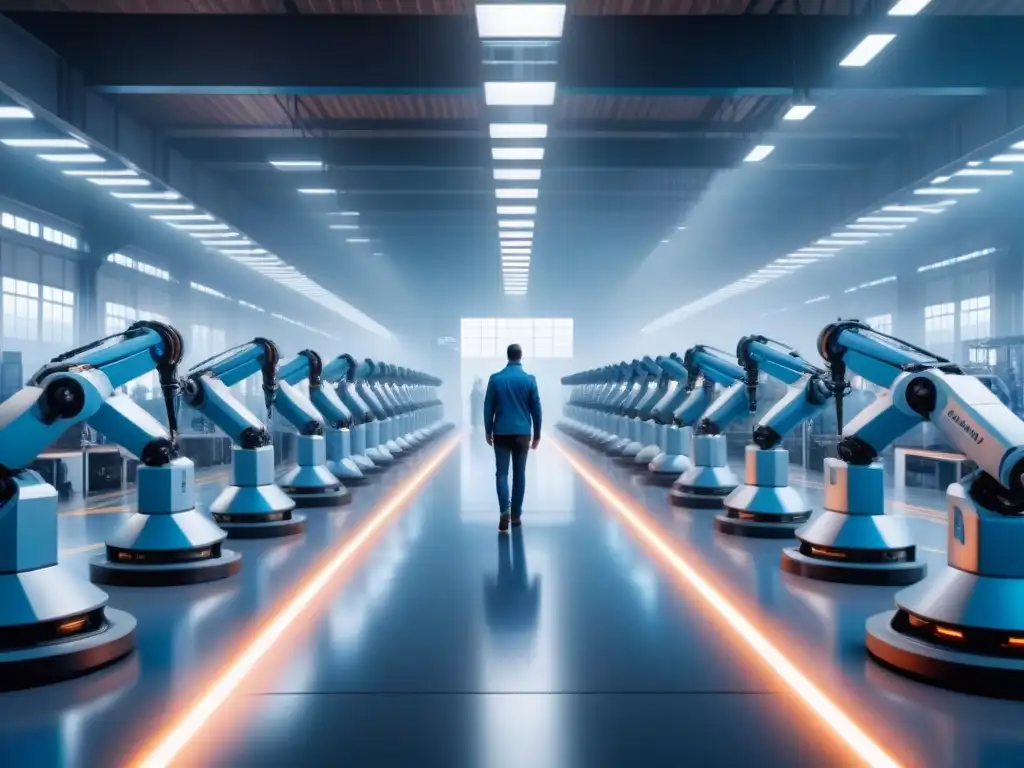
En la actualidad, la industria manufacturera se encuentra en constante evolución, buscando formas de mejorar la eficiencia, reducir costos y optimizar los procesos de producción. En este contexto, la implementación de técnicas de Lean Manufacturing ha cobrado relevancia como una estrategia efectiva para lograr estos objetivos. Lean Manufacturing se enfoca en eliminar desperdicios y optimizar recursos, lo que resulta en una producción más eficiente y rentable.
La integración de sistemas es un componente clave en el proceso de mejora continua de la manufactura. La capacidad de integrar de manera efectiva diferentes sistemas y procesos en una línea de producción puede marcar la diferencia en términos de competitividad y éxito en el mercado. La adopción de tecnologías de integración para manufactura se ha convertido en una prioridad para muchas empresas que buscan mantenerse a la vanguardia en un entorno altamente competitivo.
En este contexto, la combinación de Lean Manufacturing con tecnologías de integración para manufactura promete ser una estrategia poderosa para mejorar la eficiencia y la productividad en la industria. La implementación de sistemas integrados basados en Lean Manufacturing puede ayudar a reducir los tiempos de entrega, minimizar los costos de producción y mejorar la calidad de los productos finales.
Impacto de la Inteligencia Artificial y la Automatización en Lean Manufacturing
La Inteligencia Artificial (IA) y la automatización juegan un papel fundamental en la evolución de Lean Manufacturing y su integración con otros sistemas. La IA permite la optimización de procesos, la detección de patrones y la toma de decisiones basadas en datos en tiempo real. Esto facilita la identificación de áreas de mejora y la implementación de soluciones más eficientes en el entorno de producción.
Por otro lado, la automatización de procesos a través de tecnologías como la robótica y los sistemas de control automatizado contribuye a la reducción de tiempos de ciclo, la minimización de errores y la mejora de la precisión en las operaciones. La combinación de IA y automatización con los principios de Lean Manufacturing puede resultar en una mayor eficiencia operativa y una mayor competitividad en el mercado.
La integración de Lean Manufacturing con tecnologías avanzadas como la Inteligencia Artificial y la automatización promete revolucionar la industria manufacturera, permitiendo a las empresas alcanzar niveles de eficiencia y productividad nunca antes vistos. Aquellas organizaciones que logren aprovechar al máximo estas tecnologías estarán mejor posicionadas para competir en un mercado global cada vez más exigente.
Conclusión: Maximizando el Potencial de Lean Manufacturing para una Integración de Sistemas Efectiva
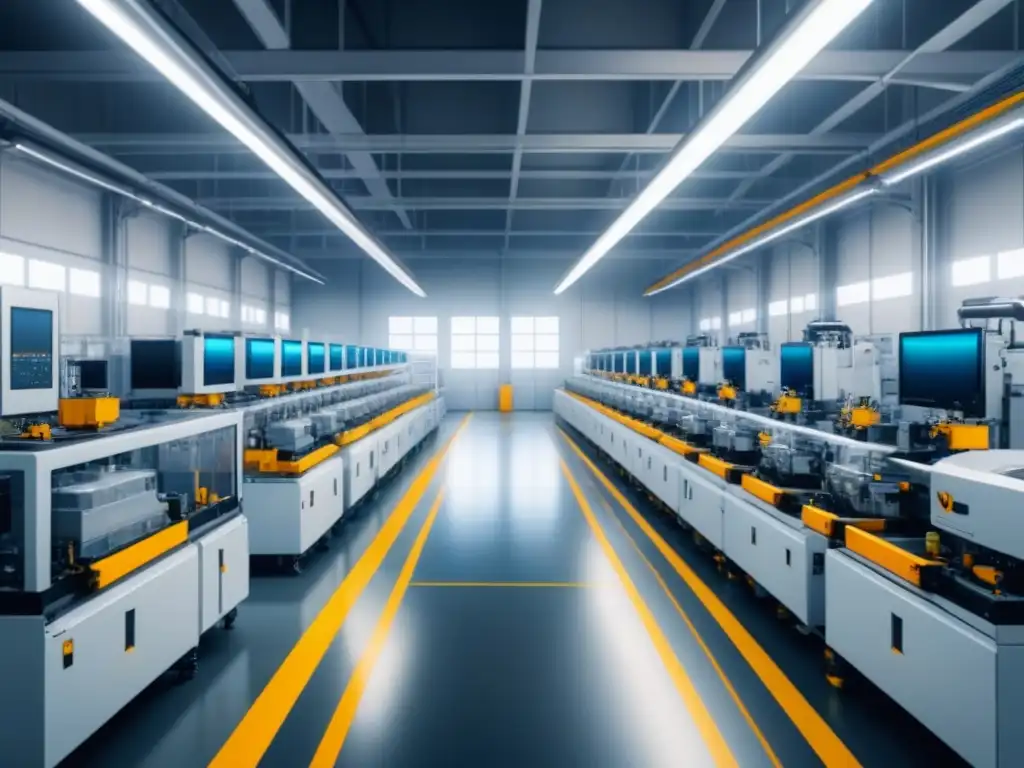
La implementación de técnicas de Lean Manufacturing en el proceso de integración de sistemas ha demostrado ser un factor clave para mejorar la eficiencia y la productividad en diversas industrias. Al adoptar un enfoque Lean, las organizaciones pueden reducir el desperdicio, optimizar los procesos y mejorar la calidad de sus productos, lo que a su vez contribuye a una integración de sistemas más efectiva.
La filosofía de Lean Manufacturing se basa en la eliminación de actividades que no agregan valor, lo que resulta en una producción más ágil y flexible. Al aplicar estos principios a la integración de sistemas, las empresas pueden minimizar los tiempos de inactividad, reducir los costos y aumentar la satisfacción del cliente al ofrecer productos y servicios de alta calidad de manera más eficiente.
Además, al combinar Lean Manufacturing con tecnologías de integración avanzadas, como IoT, IA y sistemas ciberfísicos, las organizaciones pueden alcanzar un nivel superior de eficiencia y competitividad en un mercado cada vez más globalizado y exigente.
Preguntas frecuentes
1. ¿Qué es Lean Manufacturing y por qué es importante en la integración de sistemas?
La Lean Manufacturing se enfoca en eliminar desperdicios y optimizar procesos para mejorar la eficiencia. En la integración de sistemas, ayuda a sincronizar operaciones de manera efectiva.
2. ¿Cuál es el impacto de las técnicas de Lean Manufacturing en la productividad de una empresa?
Las técnicas de Lean Manufacturing pueden aumentar la productividad al reducir tiempos de espera y mejorar la calidad de los productos, lo que lleva a una mayor eficiencia.
3. ¿Cómo pueden las empresas implementar con éxito Lean Manufacturing en sus operaciones?
La implementación exitosa de Lean Manufacturing requiere un compromiso desde la alta dirección, la formación adecuada del personal y la mejora continua de los procesos.
4. ¿Qué beneficios puede obtener una empresa al integrar Lean Manufacturing en sus sistemas?
La integración de Lean Manufacturing puede resultar en una reducción de costos, una mayor satisfacción del cliente y una mejor competitividad en el mercado.
5. ¿Cuál es el rol de la tecnología en la aplicación de Lean Manufacturing en la integración de sistemas?
La tecnología juega un papel clave al facilitar la automatización de procesos, la recopilación de datos en tiempo real y la visualización de la información para la toma de decisiones basadas en datos en un entorno de integración de sistemas.
Reflexión final: El Impacto Duradero de las Técnicas de Lean Manufacturing en la Integración de Sistemas
En un mundo cada vez más interconectado y tecnológicamente avanzado, la aplicación de las técnicas de Lean Manufacturing en la integración de sistemas se vuelve no solo relevante, sino crucial para la eficiencia y competitividad de las organizaciones en la actualidad.
La influencia del Lean Manufacturing en la integración de sistemas no solo ha transformado la forma en que las empresas operan, sino que también ha dejado una huella profunda en la cultura empresarial y en la sociedad en general. "La excelencia no es un acto, sino un hábito", nos recuerda Aristóteles, resaltando la importancia de la constancia y la mejora continua en la implementación de estas técnicas.
.
Invitamos a cada individuo y organización a reflexionar sobre cómo pueden aplicar los principios del Lean Manufacturing en sus propias prácticas y procesos, con el objetivo de alcanzar una integración de sistemas más efectiva y sostenible en el tiempo.
¡Únete a la revolución con Innovación Industrial!
Querido lector de Innovación Industrial, ¡Gracias por ser parte de nuestra comunidad apasionada por la innovación en la industria! Te invitamos a compartir este artículo sobre el impacto de las técnicas de Lean Manufacturing en la integración de sistemas en tus redes sociales para inspirar a más personas a explorar este tema. ¿Qué otros temas te gustaría ver en nuestros próximos artículos? ¡Déjanos tus comentarios y experiencias debajo! ¡Juntos podemos contribuir al avance de la industria!
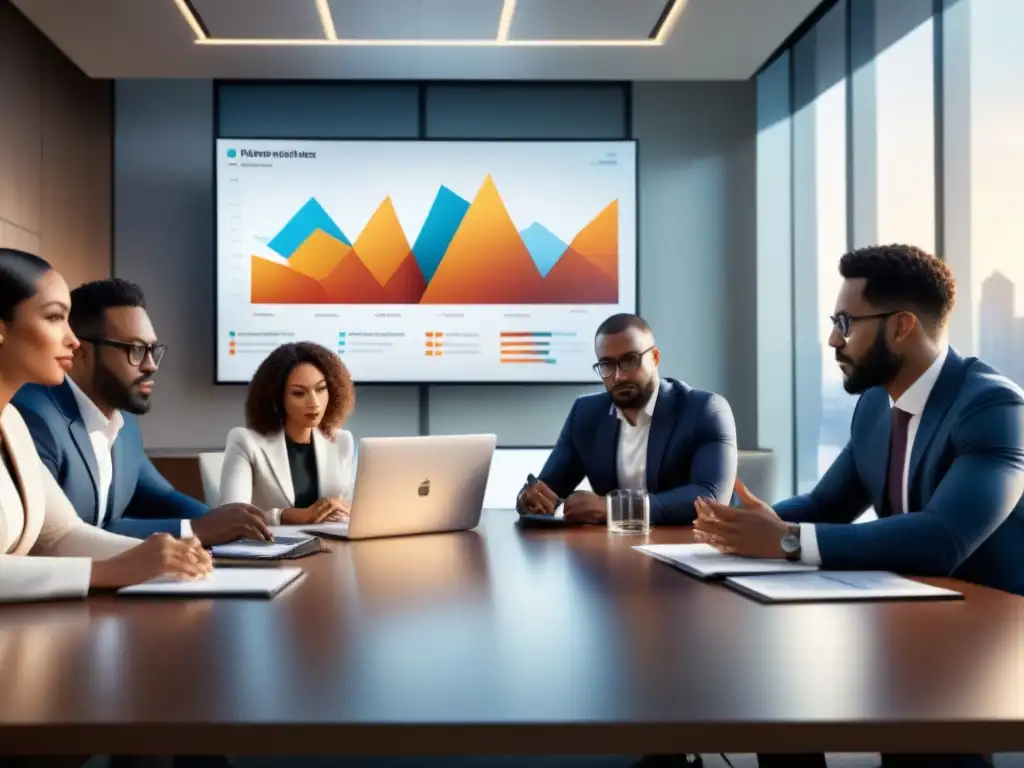
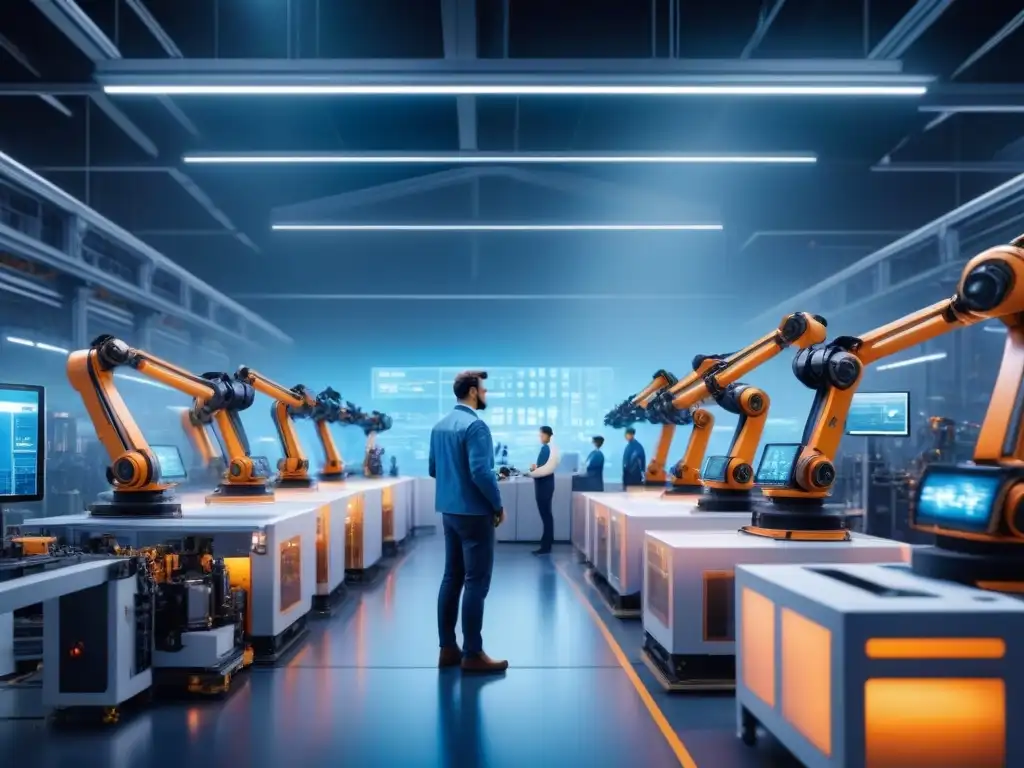
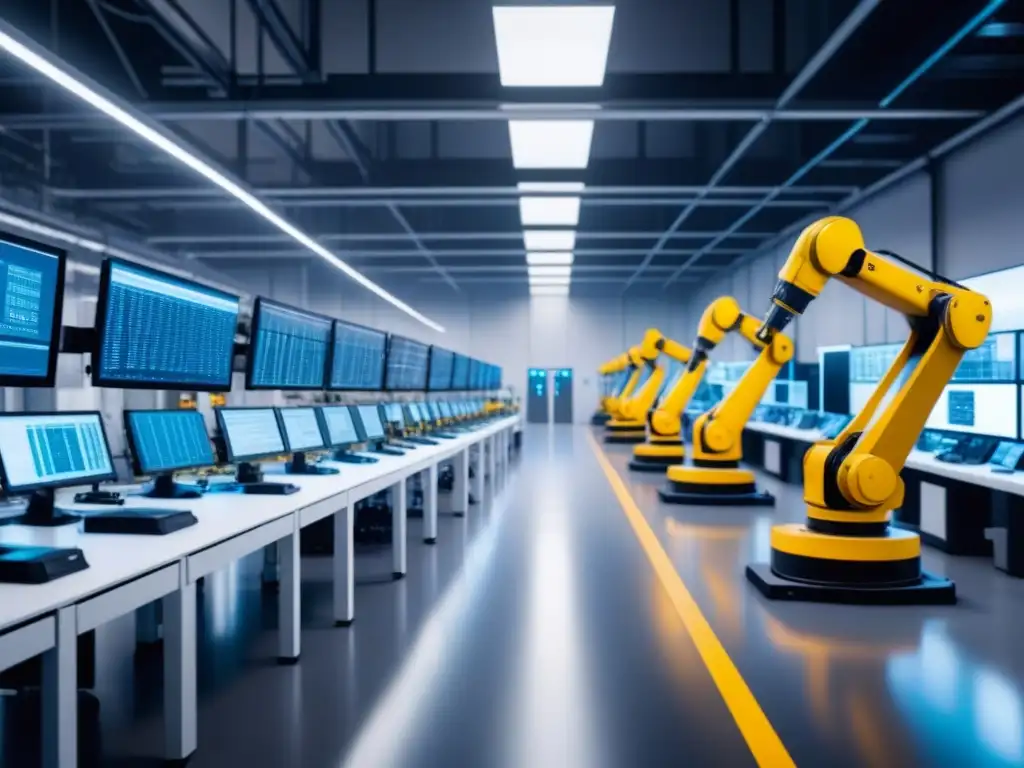
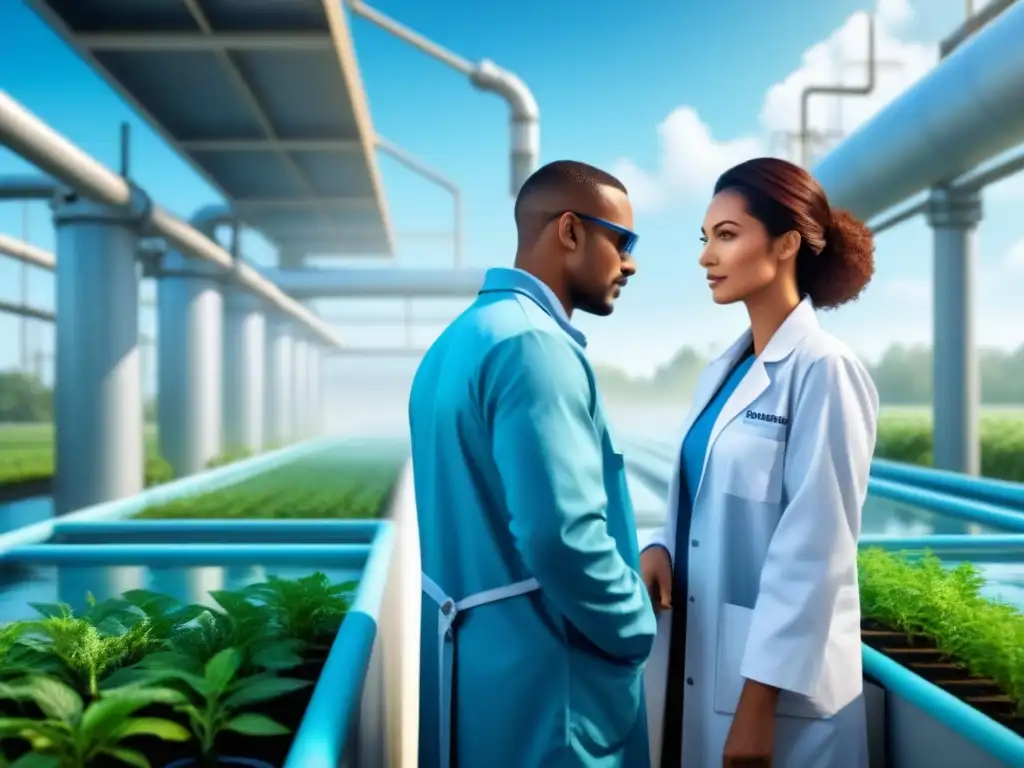
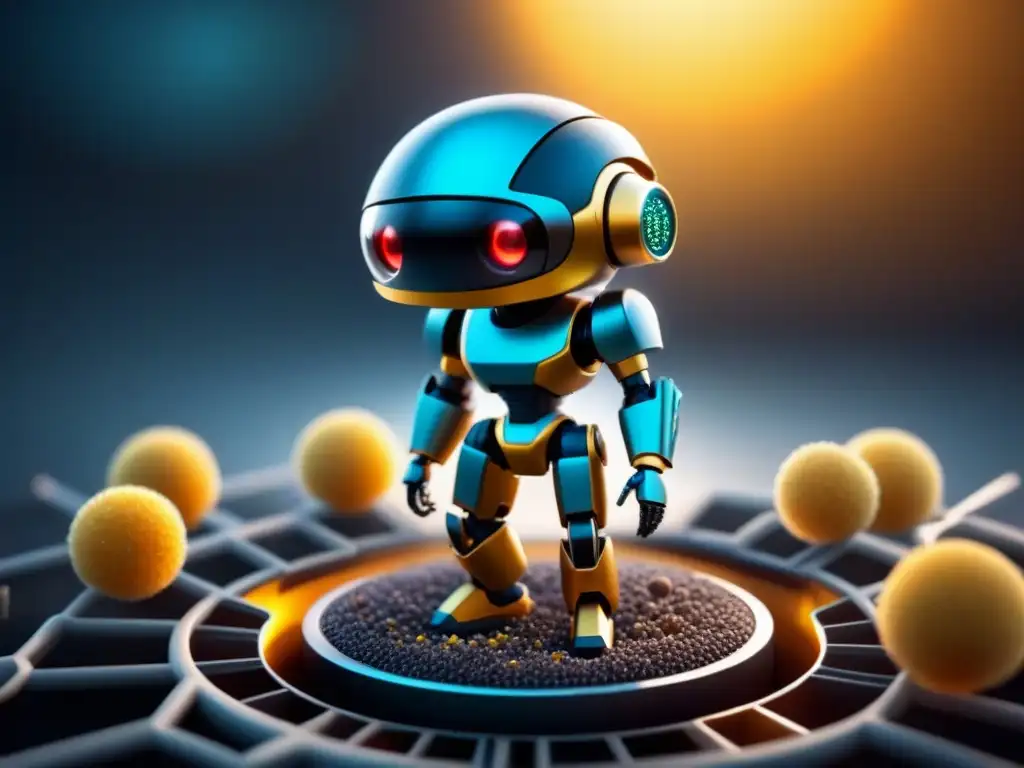
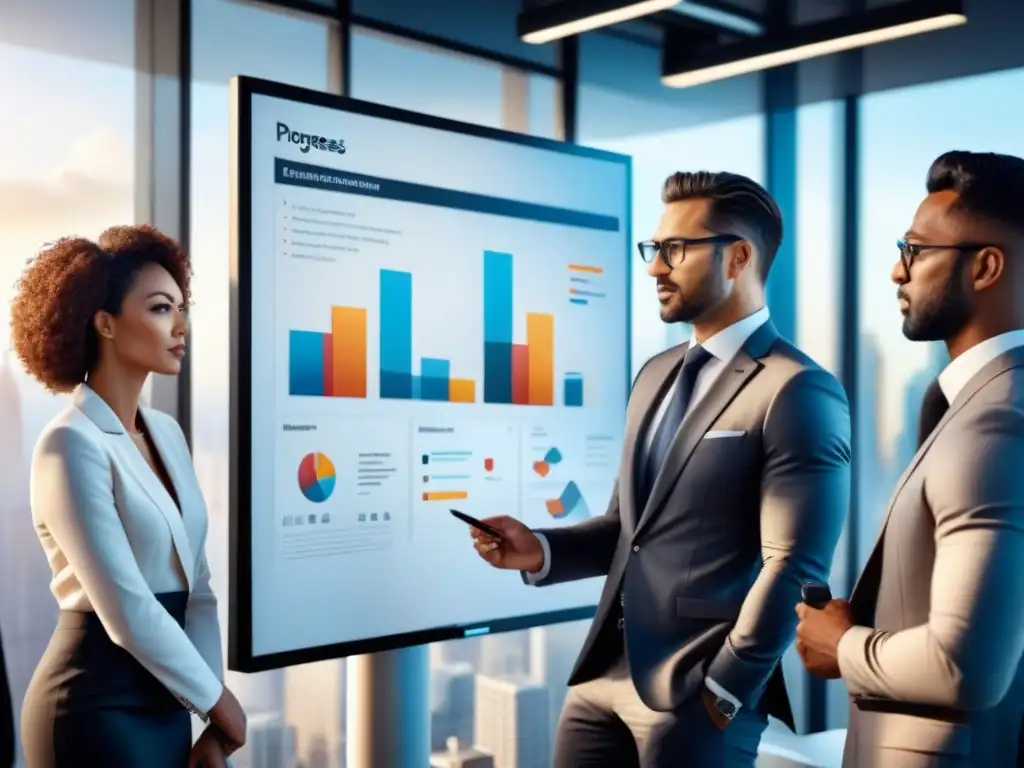
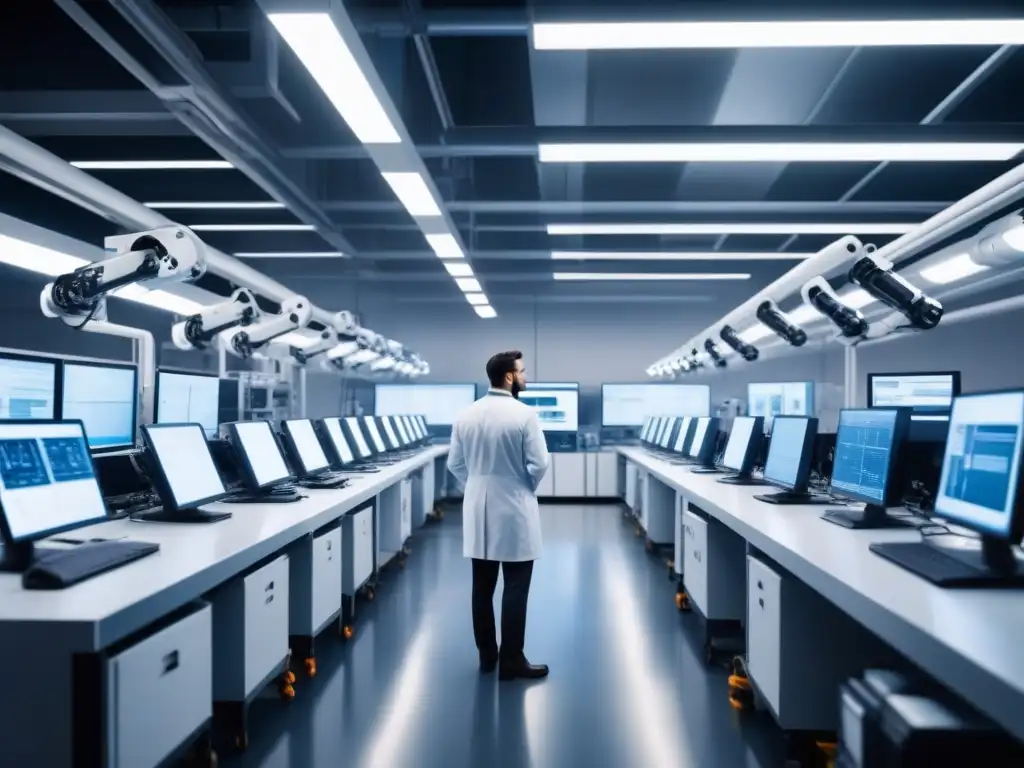
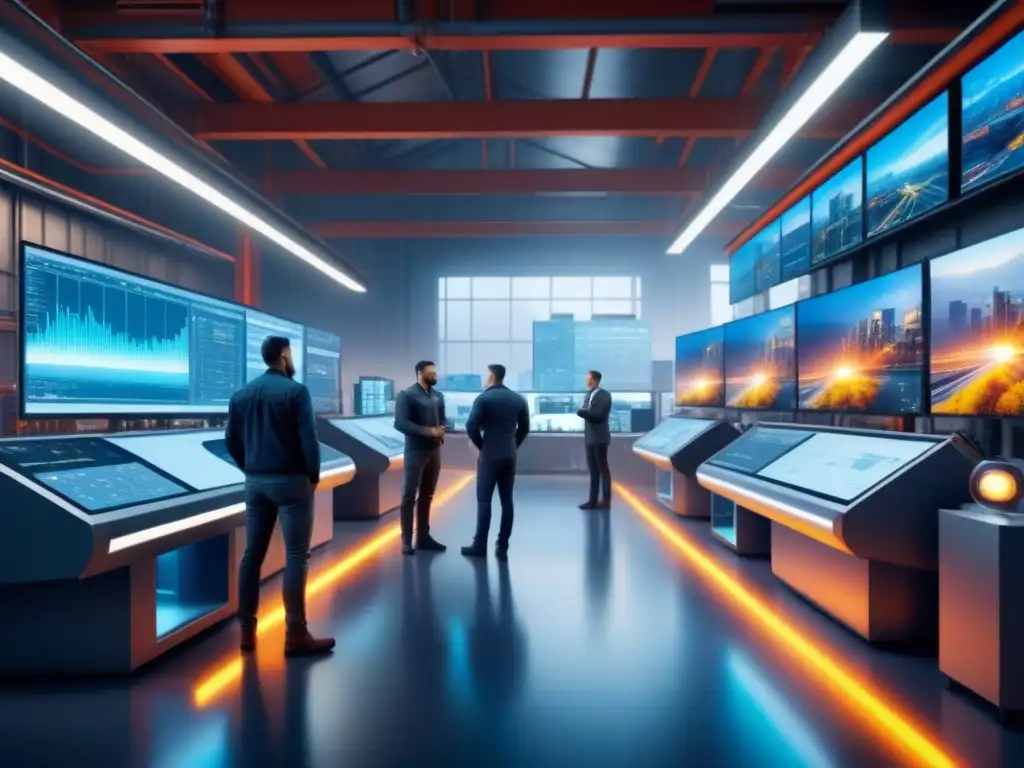
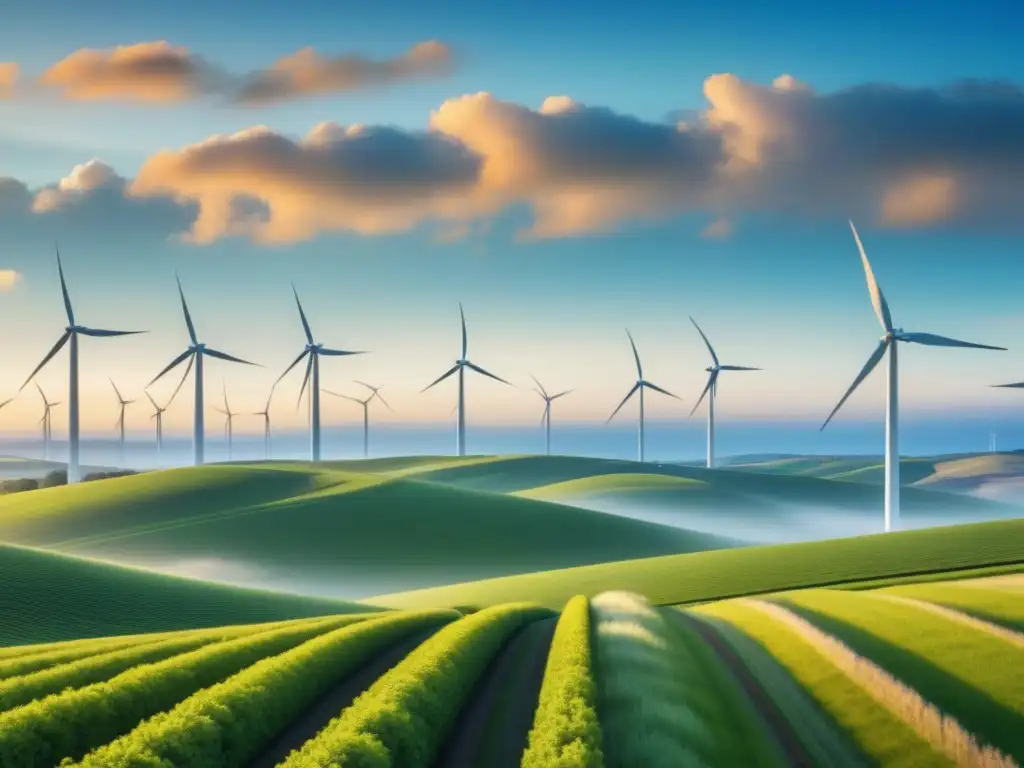
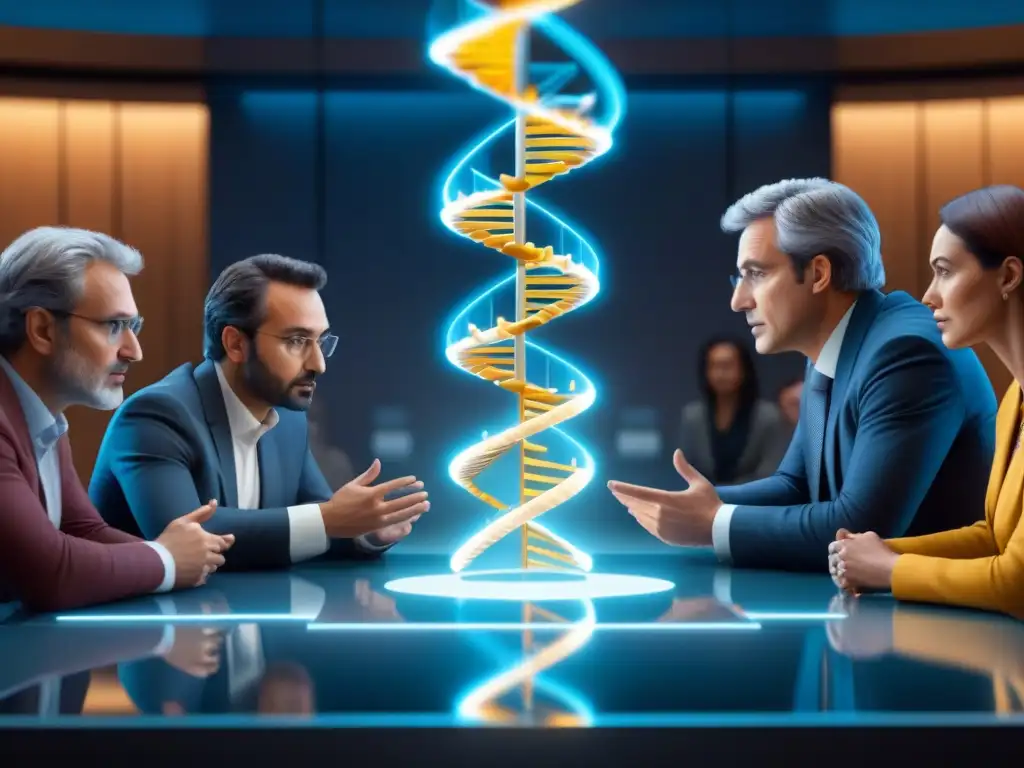
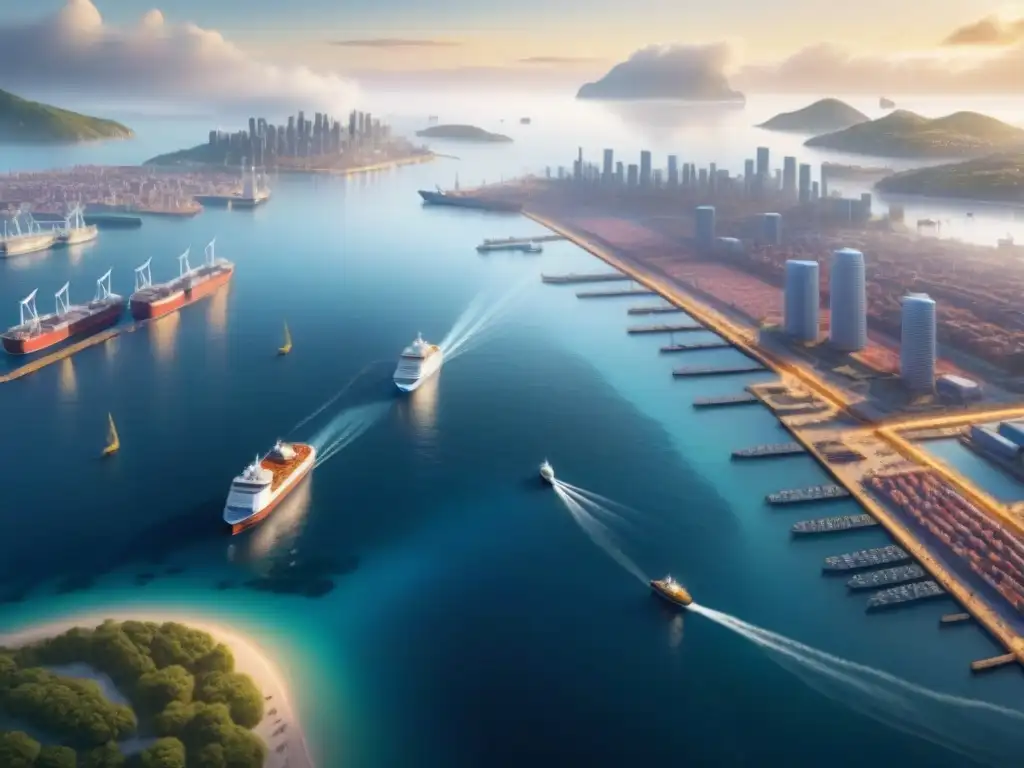
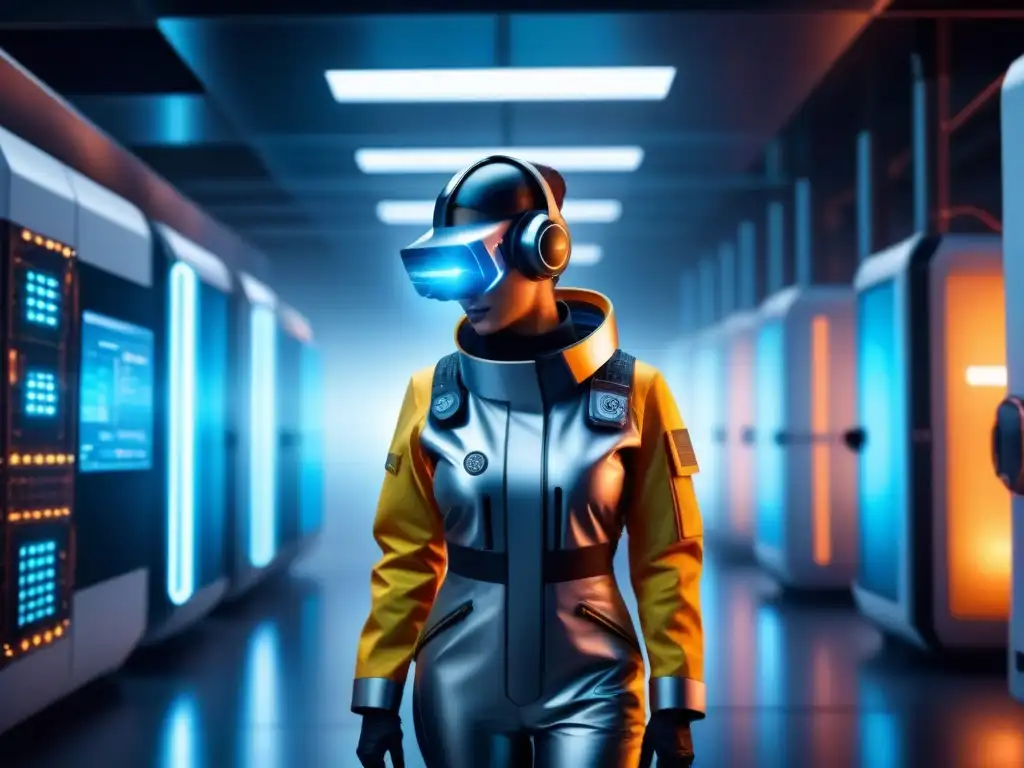
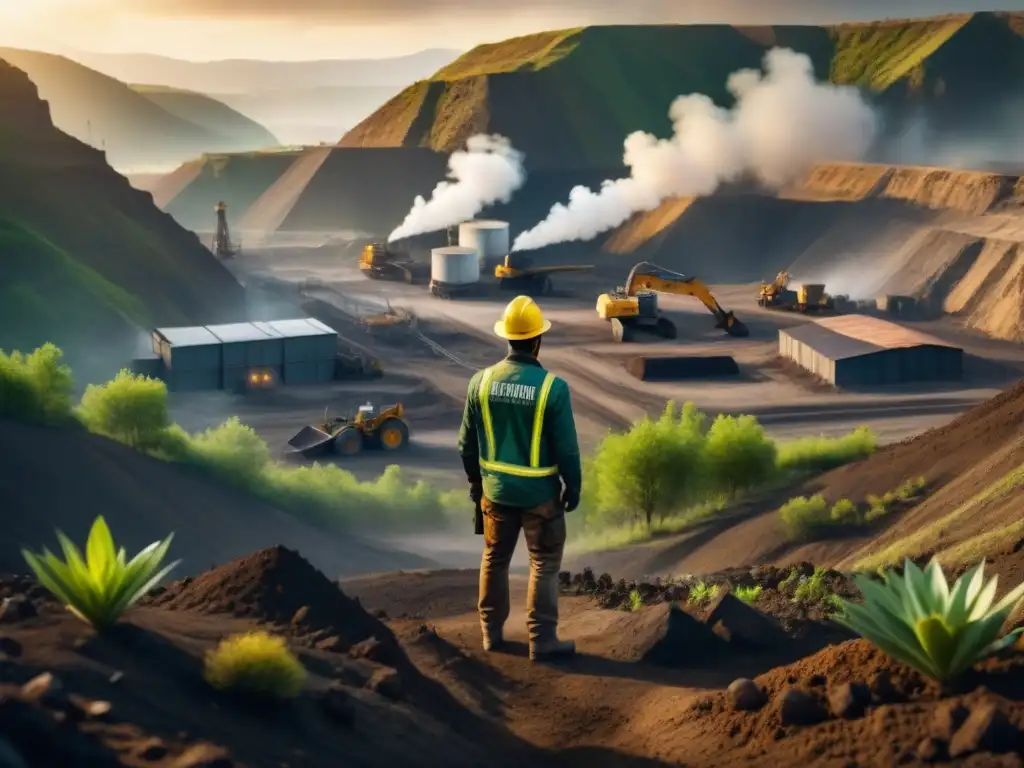
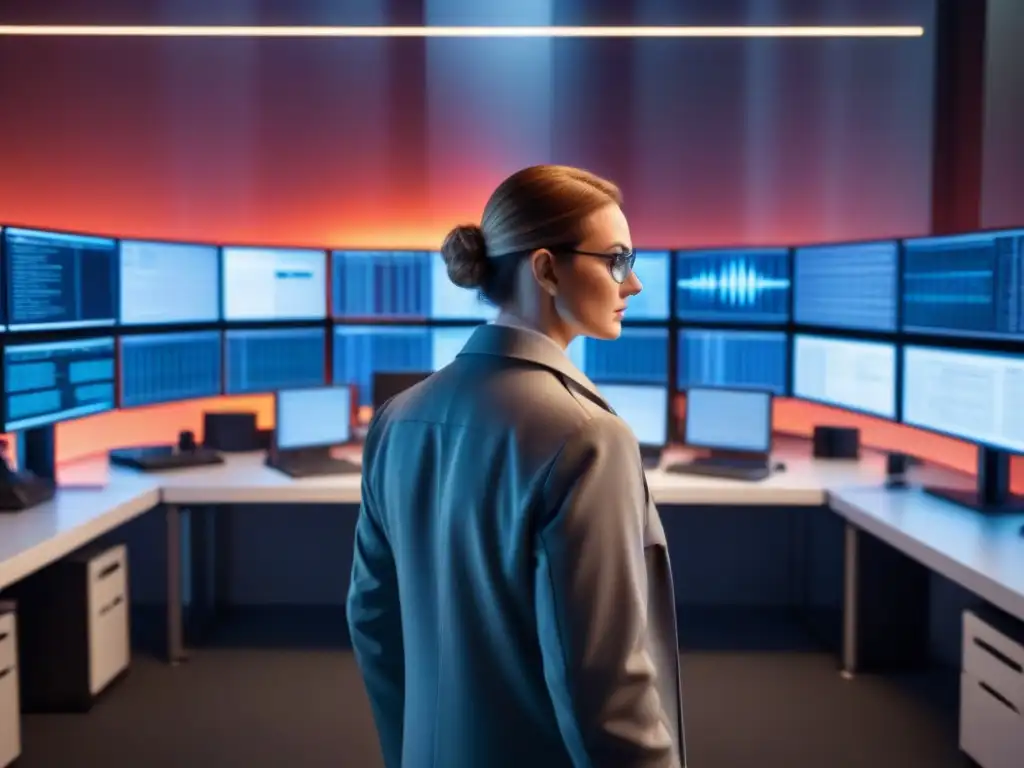
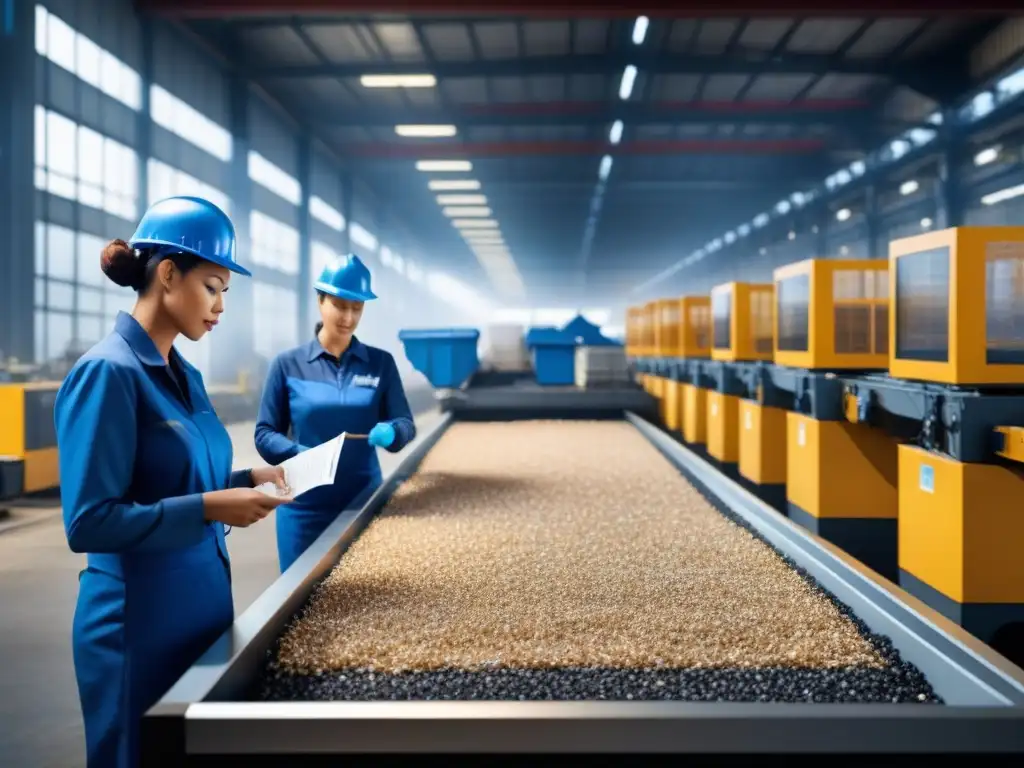
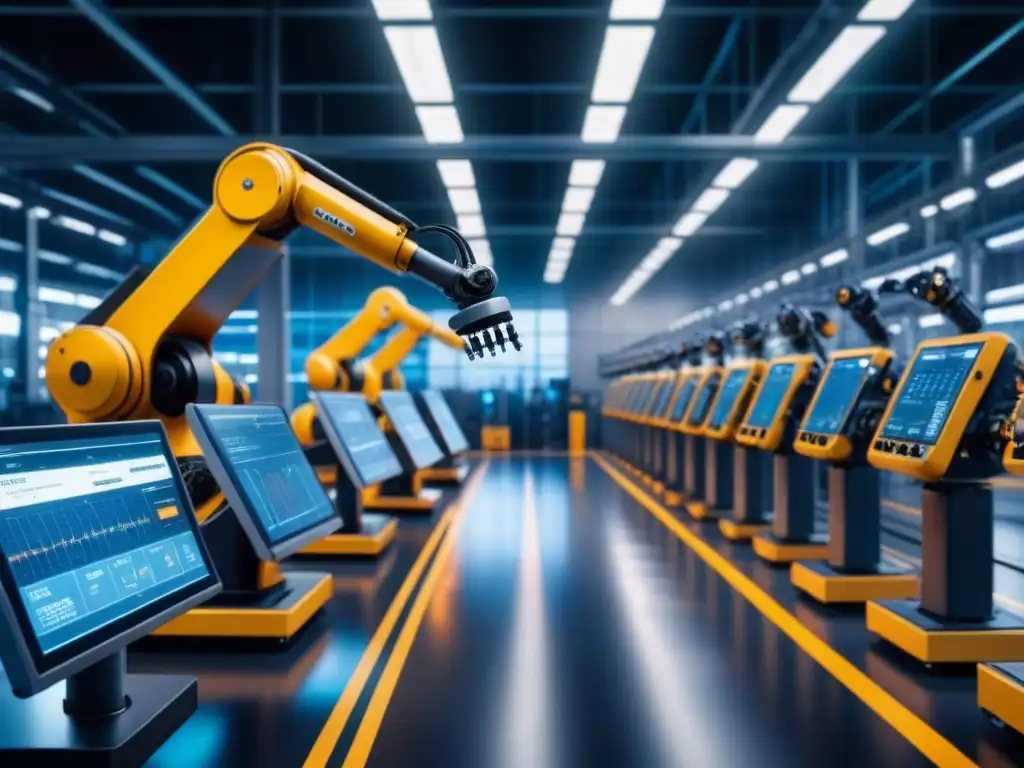
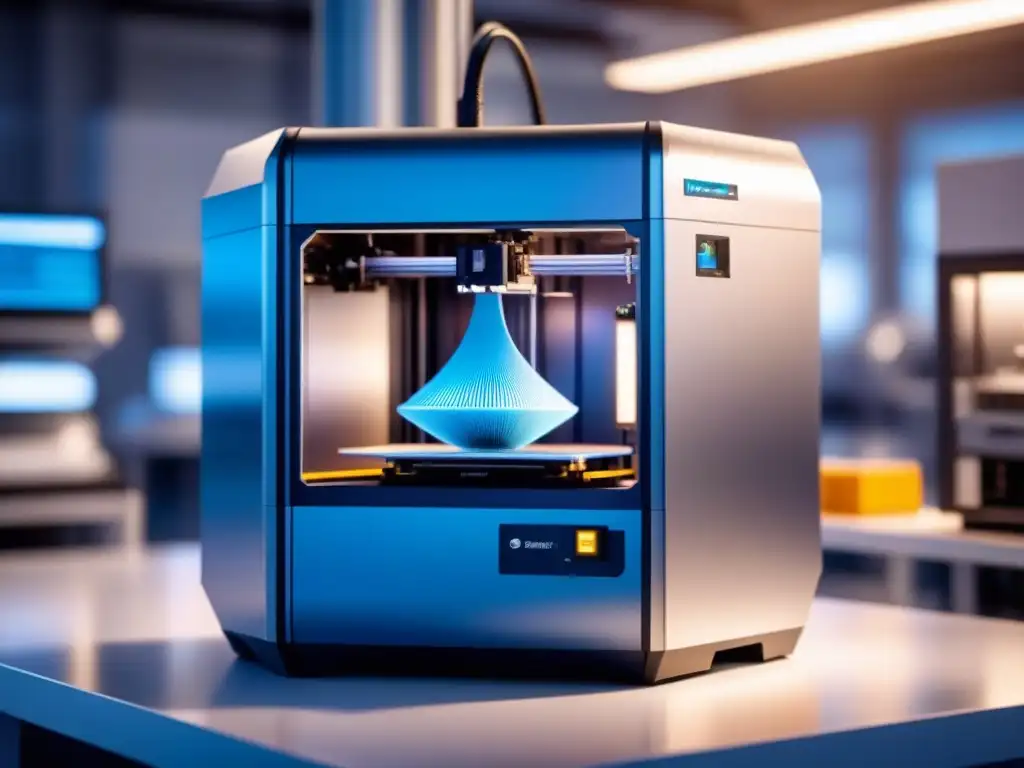
Si quieres conocer otros artículos parecidos a Lean and Mean: The Impact of Lean Manufacturing Techniques on System Integration puedes visitar la categoría Integración de Sistemas.
Deja una respuesta
Articulos relacionados: