El análisis predictivo en mantenimiento: Un aliado contra el desgaste y la obsolescencia de maquinaria
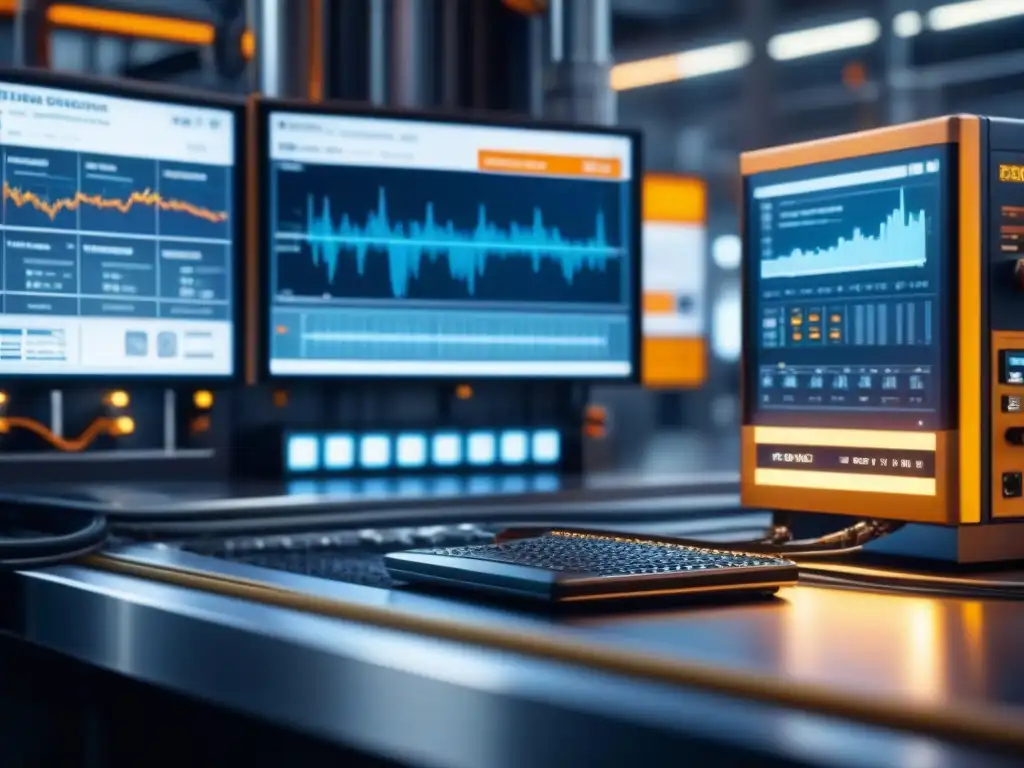
¡Bienvenidos a Innovación Industrial! Sumérgete en el fascinante mundo de los avances tecnológicos en diversas industrias. Descubre cómo el análisis predictivo en mantenimiento se convierte en un aliado crucial contra el desgaste y la obsolescencia de maquinaria en nuestro artículo principal: "El análisis predictivo en mantenimiento: Un aliado contra el desgaste y la obsolescencia de maquinaria". ¡Explora, aprende y déjate sorprender por la innovación industrial!
- Introducción al análisis predictivo en el mantenimiento de maquinaria
- Componentes clave del análisis predictivo en mantenimiento
- Casos de éxito: Aplicación del análisis predictivo en diferentes industrias
- Beneficios concretos del análisis predictivo en el mantenimiento
- Herramientas y software líderes en análisis predictivo
- Desafíos y consideraciones para la implementación exitosa
- El futuro del análisis predictivo en el mantenimiento de maquinaria
- Conclusión
-
Preguntas frecuentes
- 1. ¿Qué es el análisis predictivo en mantenimiento de maquinaria?
- 2. ¿Cuál es la importancia del análisis predictivo en la industria?
- 3. ¿Cómo se implementa el análisis predictivo en el mantenimiento de maquinaria?
- 4. ¿Qué beneficios aporta el análisis predictivo en el mantenimiento industrial?
- 5. ¿Cuál es el rol de la tecnología en el análisis predictivo en mantenimiento?
- Reflexión final: El poder del análisis predictivo en el mantenimiento de maquinaria
Introducción al análisis predictivo en el mantenimiento de maquinaria
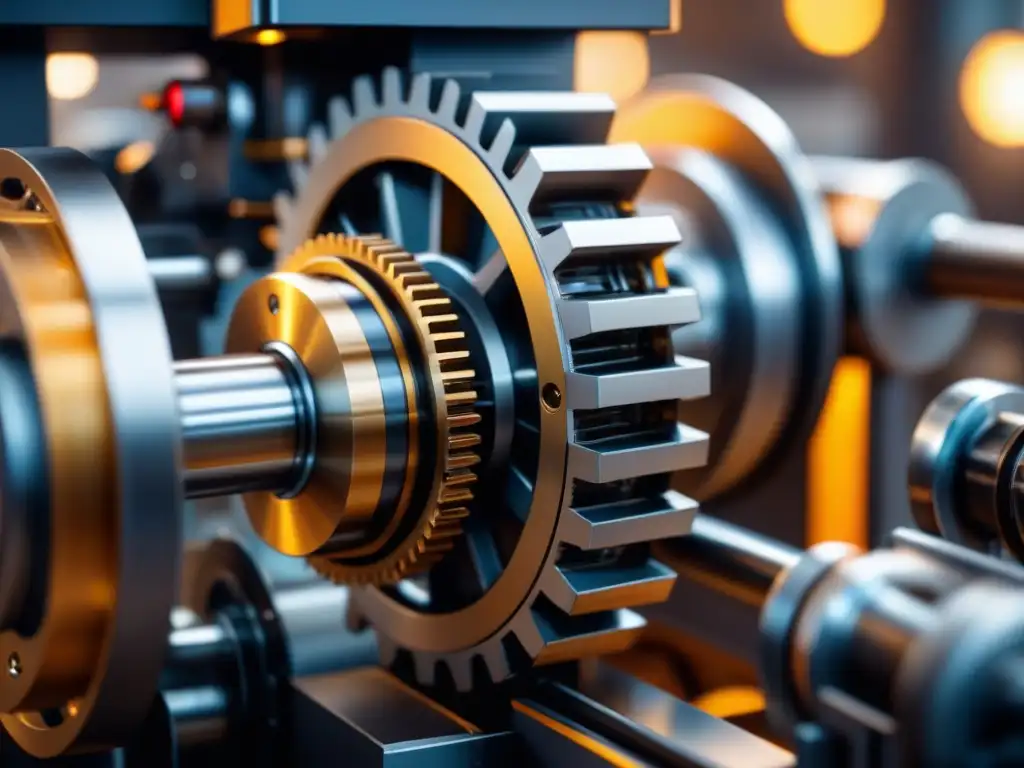
El análisis predictivo en el mantenimiento de maquinaria es una técnica que utiliza datos históricos y modelos estadísticos para predecir cuándo es probable que ocurran fallos en equipos industriales. Este enfoque se basa en la idea de que, mediante el monitoreo continuo de variables relevantes, se pueden identificar patrones y anomalías que indiquen un posible deterioro o avería en la maquinaria.
Al aplicar el análisis predictivo en el mantenimiento de maquinaria, las empresas pueden anticiparse a los problemas potenciales, programar intervenciones de mantenimiento de manera más eficiente y reducir los tiempos de inactividad no planificados. Esto se traduce en un ahorro significativo de costos y una mayor disponibilidad de los activos, lo que contribuye a una operación más eficiente y rentable.
Para llevar a cabo el análisis predictivo en el mantenimiento de maquinaria, se recopilan datos de sensores, dispositivos de monitoreo y sistemas de control, que luego se analizan mediante algoritmos de aprendizaje automático y técnicas estadísticas avanzadas. Estos modelos predictivos permiten identificar tendencias, anticipar posibles fallas y tomar decisiones informadas para optimizar la gestión de activos industriales.
Componentes clave del análisis predictivo en mantenimiento
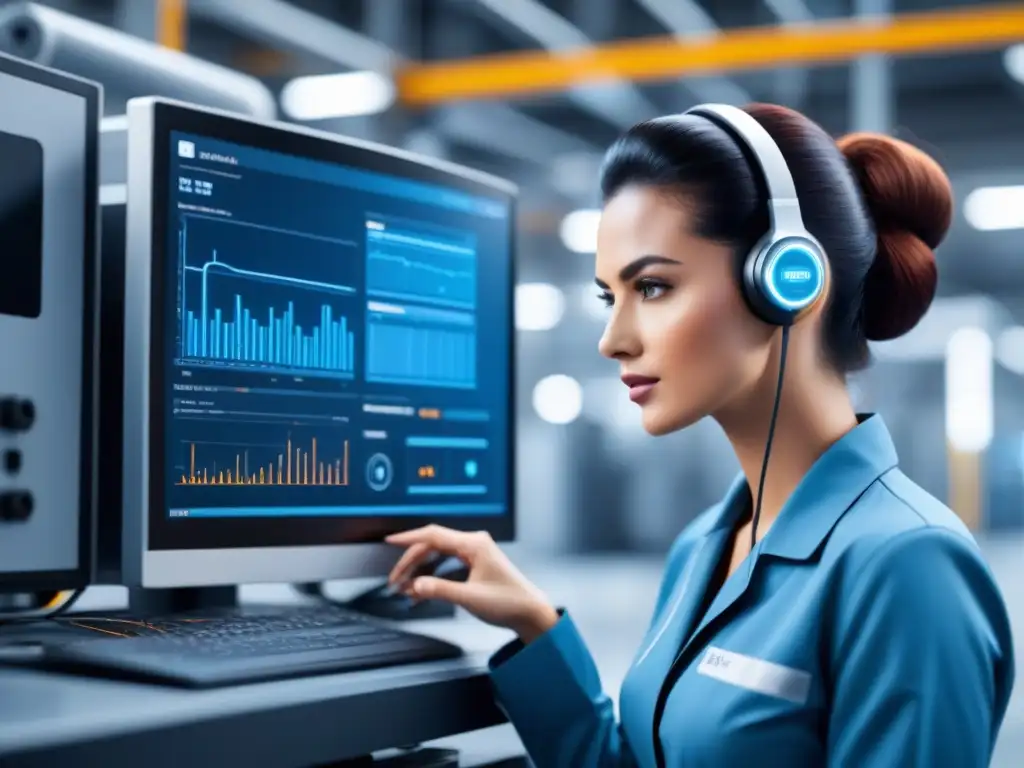
Tecnologías habilitadoras: IoT y Big Data
El análisis predictivo en mantenimiento se apoya en tecnologías clave como el Internet de las cosas (IoT) y el Big Data. El IoT permite la conectividad de dispositivos y maquinaria, recopilando datos en tiempo real sobre su funcionamiento y rendimiento. Estos datos, a su vez, son procesados y almacenados en plataformas de Big Data, donde se pueden analizar para identificar patrones y tendencias.
Gracias al IoT y al Big Data, las empresas pueden monitorear de forma proactiva el estado de su maquinaria, anticipando posibles fallas y realizando mantenimiento preventivo de manera eficiente. Esta combinación de tecnologías permite optimizar los procesos de mantenimiento y reducir costos asociados a paradas no planificadas.
La integración de IoT y Big Data en el análisis predictivo en mantenimiento es fundamental para mejorar la fiabilidad y disponibilidad de la maquinaria en diversas industrias, garantizando un funcionamiento óptimo y prolongando su vida útil.
Metodologías de análisis: Machine Learning y AI
En el contexto del análisis predictivo en mantenimiento, el Machine Learning y la Inteligencia Artificial (AI) desempeñan un papel crucial. Estas metodologías permiten a las empresas desarrollar modelos predictivos basados en datos históricos y en tiempo real, identificando anomalías y anticipando posibles problemas en la maquinaria.
El Machine Learning y la AI posibilitan la detección de patrones complejos en los datos de mantenimiento, lo que facilita la predicción de fallos y la recomendación de acciones correctivas. Estas tecnologías avanzadas mejoran la eficiencia de los procesos de mantenimiento al predecir con precisión cuándo es necesario intervenir en la maquinaria, evitando costosos tiempos de inactividad.
La aplicación de Machine Learning y AI en el análisis predictivo en mantenimiento ofrece a las empresas una ventaja competitiva al optimizar la gestión de activos y garantizar la continuidad operativa en entornos industriales exigentes.
Recopilación y gestión de datos para predicciones precisas
La recopilación y gestión adecuada de datos son fundamentales para la generación de predicciones precisas en el mantenimiento predictivo. Es esencial contar con fuentes de datos fiables y completas, que incluyan información detallada sobre el rendimiento pasado de la maquinaria, las condiciones ambientales y otros factores relevantes.
Además, la calidad de los datos y su integración en plataformas de análisis son determinantes para la efectividad de las predicciones en el mantenimiento. La correcta normalización, limpieza y enriquecimiento de los datos permiten desarrollar modelos predictivos robustos y confiables, capaces de anticipar con precisión posibles fallos en la maquinaria.
La implementación de estrategias de recopilación y gestión de datos efectivas en el análisis predictivo en mantenimiento garantiza que las decisiones de mantenimiento se basen en información sólida y relevante, contribuyendo a la optimización de los recursos y a la mejora de la eficiencia operativa.
Casos de éxito: Aplicación del análisis predictivo en diferentes industrias
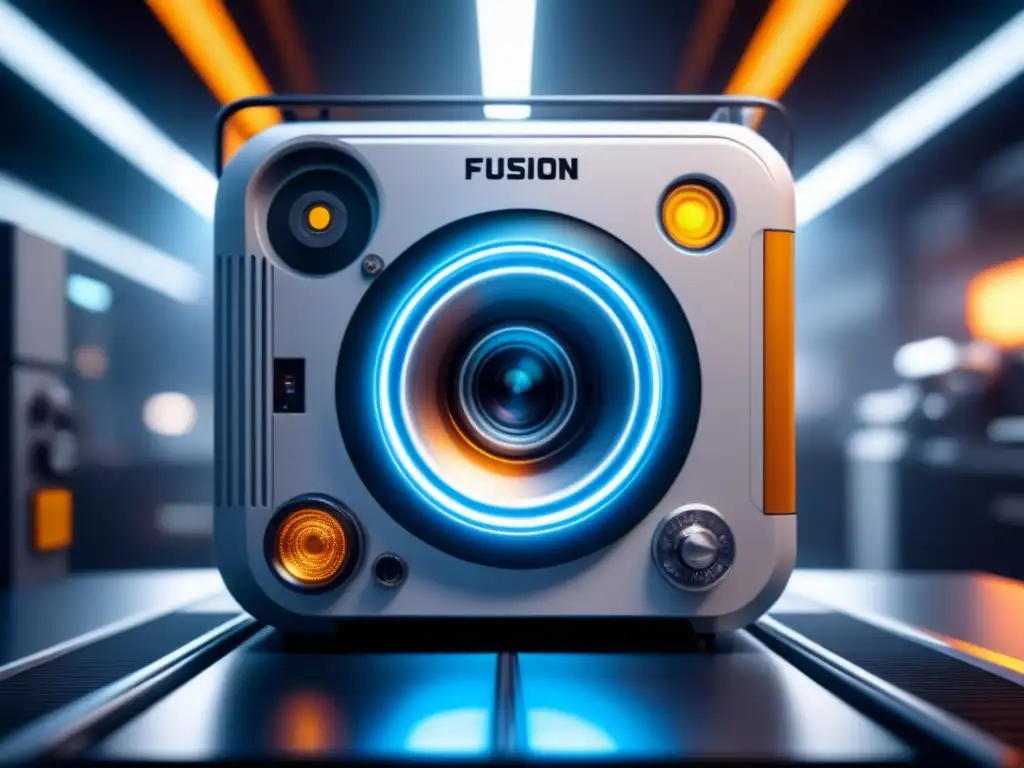
El análisis predictivo en mantenimiento ha revolucionado diversas industrias al permitir una gestión proactiva de activos, reducir costos operativos y maximizar la eficiencia de las operaciones. A continuación, se presentan ejemplos concretos de cómo esta tecnología se ha implementado con éxito en distintos sectores industriales.
Industria aeroespacial: Mantenimiento predictivo en aviones
En la industria aeroespacial, el mantenimiento predictivo se ha convertido en un aliado fundamental para garantizar la seguridad de las aeronaves y optimizar la disponibilidad de la flota. Mediante el monitoreo constante de variables como la vibración, la temperatura y la presión, las aerolíneas pueden anticipar posibles fallos en los sistemas y realizar intervenciones preventivas antes de que se produzcan averías.
Gracias al análisis predictivo, las compañías aéreas han logrado reducir significativamente los tiempos de inactividad de las aeronaves, mejorar la planificación de los mantenimientos y aumentar la vida útil de los componentes, lo que se traduce en ahorros económicos sustanciales y una mayor seguridad para los pasajeros.
Un ejemplo destacado de esta aplicación es la aerolínea Lufthansa, que ha implementado sistemas de mantenimiento predictivo en su flota de aviones, logrando una reducción del 20% en los costos de mantenimiento y una mejora del 30% en la eficiencia operativa.
Manufactura avanzada: Extensión de la vida útil de la maquinaria
En el sector de la manufactura avanzada, el análisis predictivo se ha convertido en una herramienta indispensable para prevenir averías en maquinaria, optimizar los procesos de producción y prolongar la vida útil de los equipos. Mediante la monitorización en tiempo real de variables como la temperatura, la presión y la velocidad de funcionamiento, las empresas pueden identificar patrones de desgaste y anticiparse a posibles fallos.
Empresas como Siemens y General Electric han implementado soluciones de mantenimiento predictivo en sus plantas de producción, lo que les ha permitido reducir los tiempos de inactividad de las máquinas, mejorar la calidad de los productos fabricados y aumentar la productividad en sus instalaciones.
Gracias al análisis predictivo, estas compañías han logrado incrementar la eficiencia de sus operaciones en un 15% en promedio, reducir los costos de mantenimiento en un 20% y mejorar la satisfacción de sus clientes al garantizar la continuidad de la producción.
Minería sostenible: Prevención de fallas y reducción de paradas
En el sector de la minería, el mantenimiento predictivo ha permitido a las empresas prevenir fallas en los equipos, optimizar la planificación de las operaciones y reducir los tiempos de inactividad de las minas. Mediante la monitorización en tiempo real de variables como la temperatura, la humedad y la carga de trabajo de los equipos, las compañías mineras pueden identificar posibles problemas y tomar medidas correctivas de manera anticipada.
Compañías como BHP Billiton y Rio Tinto han implementado sistemas de análisis predictivo en sus operaciones mineras, logrando reducir los costos de mantenimiento en un 25%, aumentar la productividad de las minas en un 30% y mejorar la seguridad de los trabajadores al evitar accidentes relacionados con fallos en la maquinaria.
Gracias al mantenimiento predictivo, estas empresas han podido optimizar sus procesos de extracción, reducir su impacto ambiental y garantizar la sostenibilidad a largo plazo de sus operaciones mineras.
Beneficios concretos del análisis predictivo en el mantenimiento
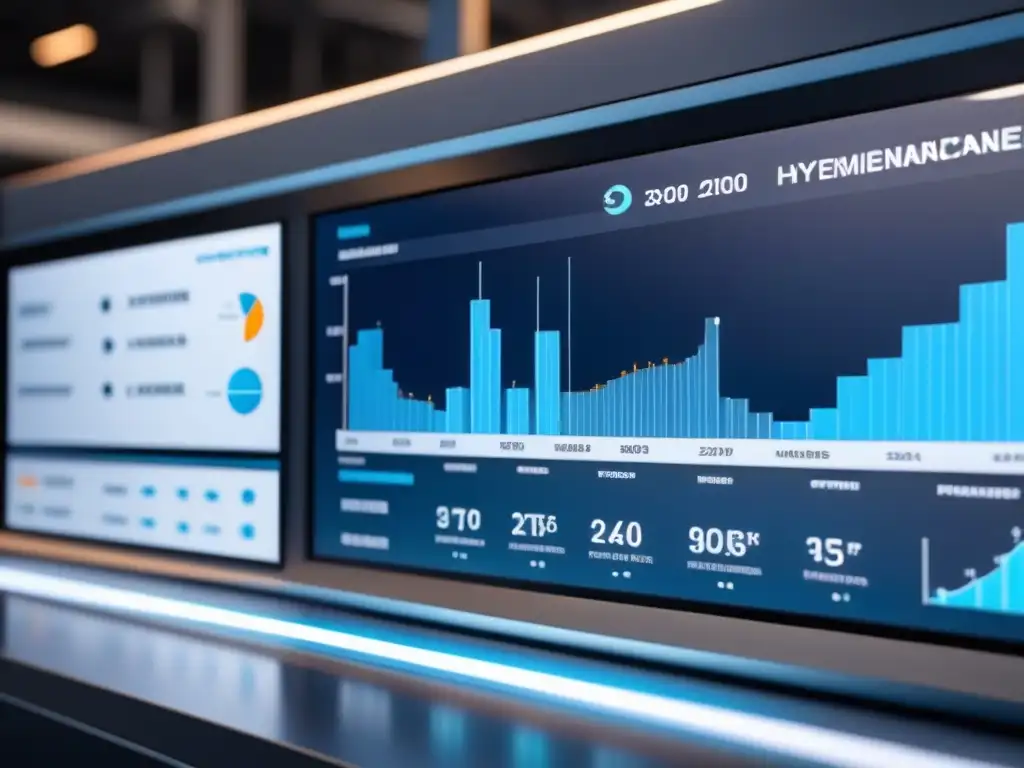
Reducción de costos operativos y de mantenimiento
Uno de los beneficios más destacados del análisis predictivo en el mantenimiento de maquinaria es la reducción significativa de los costos operativos y de mantenimiento. Al implementar esta tecnología, las empresas pueden identificar de manera anticipada posibles fallas en los equipos, lo que les permite programar intervenciones de mantenimiento preventivo en momentos estratégicos. Esto evita costosos tiempos de inactividad no planificados, optimiza la utilización de los recursos y minimiza los gastos asociados a reparaciones urgentes.
Un estudio realizado por la firma de consultoría McKinsey & Company reveló que las organizaciones que adoptan el análisis predictivo en el mantenimiento experimentan una reducción promedio del 12% en sus costos de mantenimiento y una disminución del 30% en los costos operativos totales.
Al utilizar algoritmos avanzados y sensores inteligentes, las empresas pueden anticiparse a posibles problemas en la maquinaria, lo que les permite planificar con eficacia las actividades de mantenimiento y sustitución de componentes, evitando interrupciones no planificadas que afecten la productividad y la rentabilidad.
Mejora en la seguridad y la eficiencia operativa
Otro beneficio clave del análisis predictivo en el mantenimiento de maquinaria es la mejora significativa en la seguridad y la eficiencia operativa. Al detectar de forma anticipada posibles fallos en los equipos, las empresas pueden garantizar un entorno de trabajo más seguro para sus empleados al reducir el riesgo de accidentes relacionados con la maquinaria.
Además, al optimizar la gestión de los activos y prevenir averías imprevistas, se logra una mayor eficiencia operativa. Las empresas pueden maximizar la vida útil de sus equipos, mejorar la calidad de los productos y servicios, y aumentar la productividad al evitar tiempos de inactividad no planificados.
Un informe de la firma de investigación de mercado MarketsandMarkets señala que la implementación del análisis predictivo en el mantenimiento puede conducir a una reducción del 40% en los accidentes laborales relacionados con la maquinaria y a un aumento del 25% en la eficiencia operativa de las instalaciones industriales.
Aumento de la disponibilidad y rendimiento de la maquinaria
El análisis predictivo en el mantenimiento de maquinaria también permite aumentar la disponibilidad y el rendimiento de los equipos al prevenir fallos inesperados y optimizar la planificación de las actividades de mantenimiento. Al anticiparse a posibles problemas, las empresas pueden programar intervenciones en momentos estratégicos, evitando tiempos de inactividad no planificados que afecten la producción.
Según un estudio de la firma de análisis de mercado Grand View Research, las organizaciones que implementan el análisis predictivo en el mantenimiento experimentan un aumento promedio del 20% en la disponibilidad de la maquinaria y una mejora del 15% en su rendimiento general.
Al maximizar la disponibilidad de los equipos y garantizar su óptimo funcionamiento, las empresas pueden cumplir con los plazos de producción, satisfacer la demanda de los clientes y mejorar su competitividad en el mercado.
Herramientas y software líderes en análisis predictivo
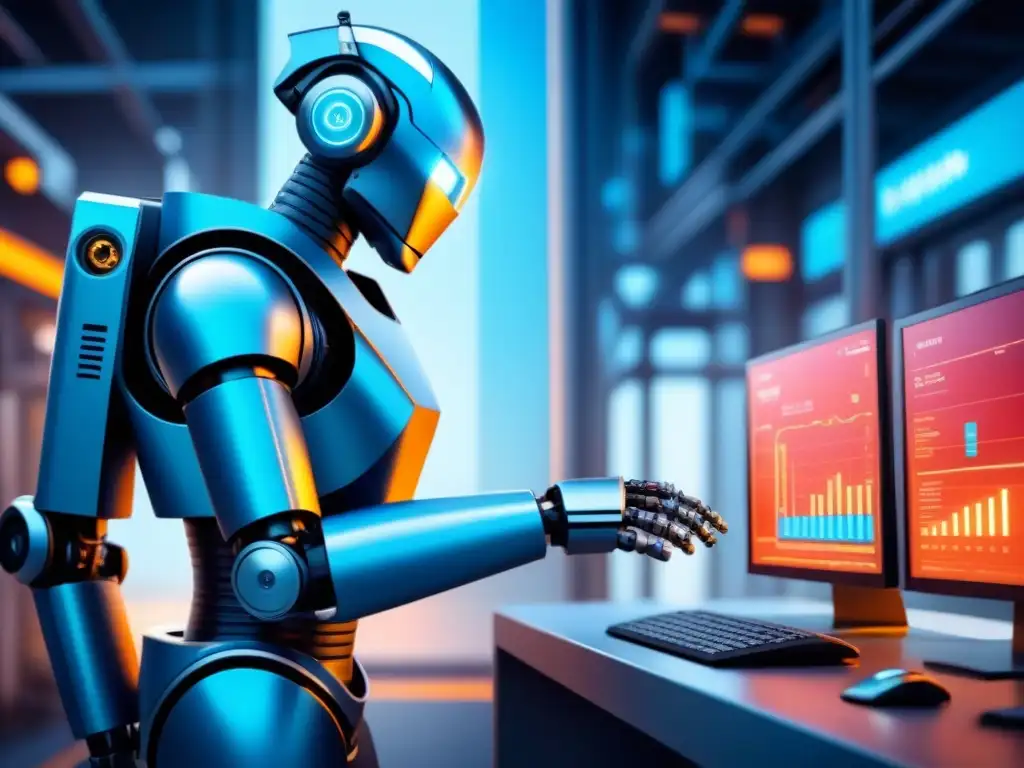
Comparativa de soluciones en el mercado
En el ámbito del análisis predictivo en mantenimiento de maquinaria, existen diversas soluciones en el mercado que ofrecen funcionalidades y características específicas para satisfacer las necesidades de las industrias. Algunas de las herramientas líderes en este campo incluyen:
- SAP Predictive Maintenance and Service: Esta solución de SAP utiliza análisis predictivos para predecir fallos en la maquinaria y optimizar las operaciones de mantenimiento. Ofrece integración con sistemas de gestión empresarial (ERP) para una visión holística de los activos.
- IBM Maximo Asset Performance Management: IBM ofrece una plataforma que combina análisis avanzados, IoT y machine learning para mejorar la eficiencia operativa y reducir los costos de mantenimiento. Permite una gestión proactiva de activos y una mayor disponibilidad de la maquinaria.
- GE Digital APM: La solución Asset Performance Management de GE Digital utiliza análisis predictivos para identificar patrones de comportamiento de los activos y prevenir fallos. Proporciona una visión en tiempo real del rendimiento de la maquinaria.
Estas herramientas ofrecen capacidades avanzadas para el análisis predictivo en mantenimiento, permitiendo a las empresas optimizar sus procesos, reducir tiempos de inactividad no planificados y mejorar la eficiencia de sus operaciones.
Integración con sistemas de gestión de mantenimiento existentes
La integración de las soluciones de análisis predictivo en mantenimiento con los sistemas de gestión de mantenimiento (CMMS) existentes es fundamental para maximizar su efectividad y facilitar la toma de decisiones informadas. Algunas consideraciones importantes para la integración incluyen:
- Interfaz de datos: Es crucial contar con una interfaz que permita la transferencia de datos entre la herramienta de análisis predictivo y el CMMS de manera eficiente y precisa.
- Compatibilidad de formatos: Los datos generados por el análisis predictivo deben ser compatibles con los formatos utilizados por el sistema de gestión de mantenimiento para una fácil interpretación y acción.
- Automatización de procesos: La automatización de procesos entre las dos plataformas puede agilizar la identificación de problemas, la asignación de tareas y la programación de mantenimiento preventivo.
Al integrar el análisis predictivo en mantenimiento con los sistemas de gestión existentes, las empresas pueden aprovechar al máximo las capacidades predictivas de las herramientas y garantizar una gestión eficiente y proactiva de sus activos.
Desafíos y consideraciones para la implementación exitosa
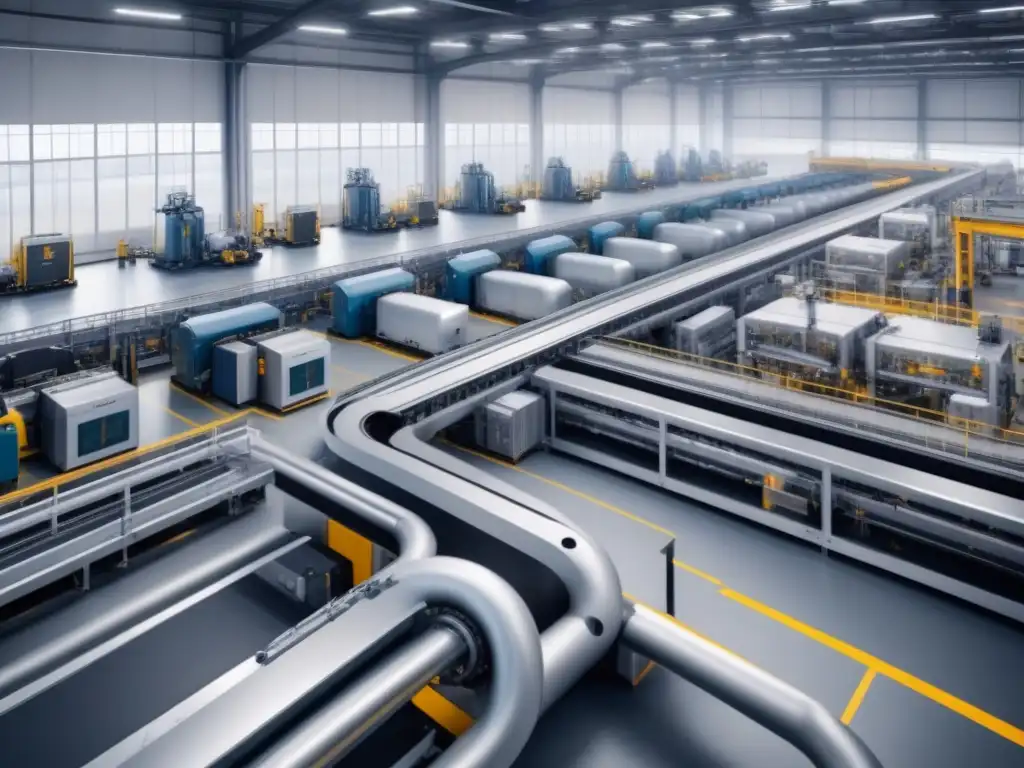
La implementación del análisis predictivo en mantenimiento puede presentar varios desafíos que las organizaciones deben abordar para garantizar su éxito y maximizar los beneficios que esta tecnología puede ofrecer. Algunos de los obstáculos más comunes incluyen:
- Falta de datos de calidad: Uno de los principales desafíos para implementar el análisis predictivo en mantenimiento es la disponibilidad de datos de calidad. Sin datos precisos y relevantes, los modelos predictivos pueden no ser efectivos.
- Integración con sistemas existentes: Otra barrera común es la integración del análisis predictivo en los sistemas de mantenimiento existentes. Asegurar la compatibilidad y la sincronización adecuada puede requerir ajustes y esfuerzos adicionales.
- Resistencia al cambio: La resistencia al cambio por parte de los empleados es otro obstáculo importante. Implementar nuevas tecnologías y procesos puede encontrarse con resistencia y es crucial abordarla mediante una adecuada gestión del cambio.
Para superar estos obstáculos y lograr una implementación exitosa del análisis predictivo en mantenimiento, las organizaciones deben considerar estrategias específicas:
- Garantizar la calidad de los datos: Es fundamental establecer procesos para recopilar, limpiar y gestionar los datos de manera eficiente, asegurando su precisión y relevancia para los modelos predictivos.
- Realizar una evaluación exhaustiva de la infraestructura tecnológica: Antes de implementar el análisis predictivo, es crucial evaluar la infraestructura tecnológica existente y realizar los ajustes necesarios para garantizar una integración efectiva.
- Comunicar de manera efectiva los beneficios: Es importante comunicar claramente a los empleados y partes interesadas los beneficios del análisis predictivo en mantenimiento, destacando cómo esta tecnología puede mejorar la eficiencia y reducir costos.
El futuro del análisis predictivo en el mantenimiento de maquinaria
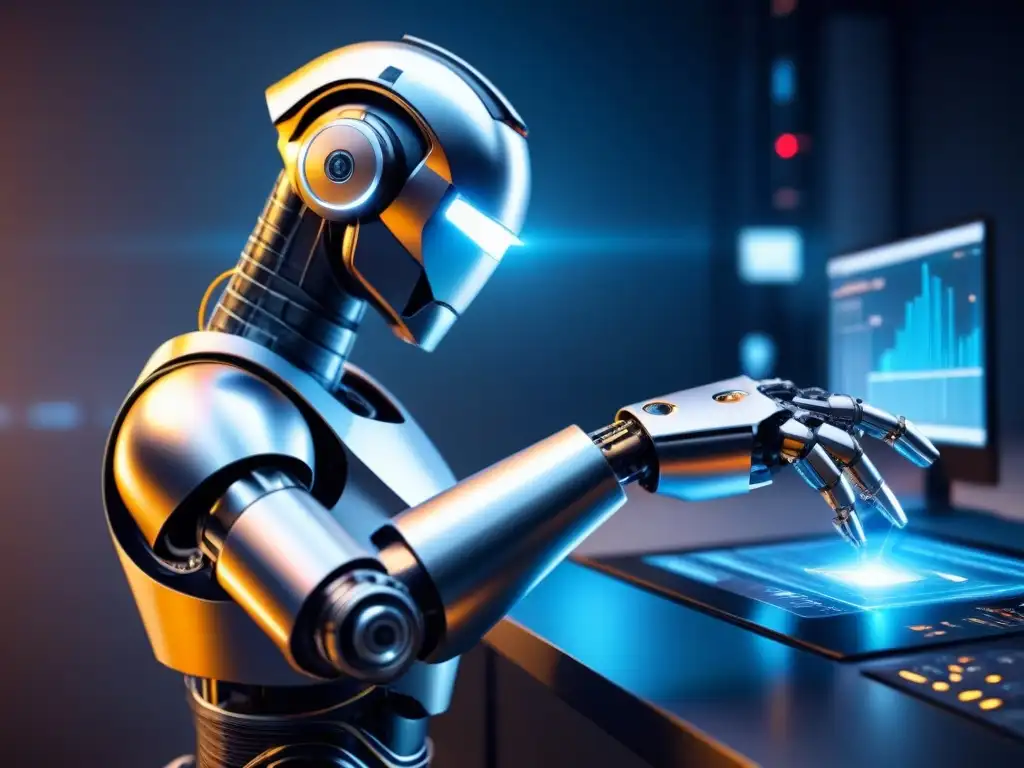
Tendencias emergentes y su impacto en la industria
En la actualidad, el análisis predictivo en el mantenimiento de maquinaria se ha convertido en una herramienta fundamental para las empresas que buscan optimizar sus procesos productivos y reducir costos operativos. Una de las tendencias emergentes más relevantes en este campo es la integración de sensores IoT (Internet de las cosas) en los equipos industriales. Estos sensores recopilan datos en tiempo real sobre el rendimiento de la maquinaria, lo que permite anticipar y prevenir posibles fallos o averías.
Otra tendencia en auge es el uso de algoritmos de machine learning y análisis de Big Data para procesar la gran cantidad de información generada por los sensores. Estas tecnologías permiten identificar patrones, tendencias y anomalías en los datos, facilitando la toma de decisiones informadas y la implementación de estrategias de mantenimiento predictivo más efectivas.
El impacto de estas tendencias en la industria es significativo, ya que contribuyen a mejorar la eficiencia operativa, prolongar la vida útil de los equipos, reducir los tiempos de inactividad no planificados y, en última instancia, aumentar la rentabilidad de las empresas.
El rol del análisis predictivo en la sostenibilidad industrial
El análisis predictivo en el mantenimiento de maquinaria desempeña un papel clave en la promoción de la sostenibilidad en la industria. Al prevenir averías y optimizar el rendimiento de los equipos, las empresas pueden reducir su consumo de recursos, minimizar la generación de residuos y disminuir su impacto ambiental.
Además, al implementar estrategias de mantenimiento predictivo, las organizaciones pueden extender la vida útil de sus activos, evitando la obsolescencia prematura de la maquinaria y reduciendo la necesidad de reemplazos frecuentes. Esto no solo resulta en un ahorro económico significativo, sino que también contribuye a una gestión más sostenible de los recursos naturales.
El análisis predictivo en el mantenimiento de maquinaria no solo beneficia a las empresas en términos de eficiencia operativa y rentabilidad, sino que también juega un papel crucial en la promoción de prácticas sostenibles y respetuosas con el medio ambiente en el sector industrial.
Conclusión
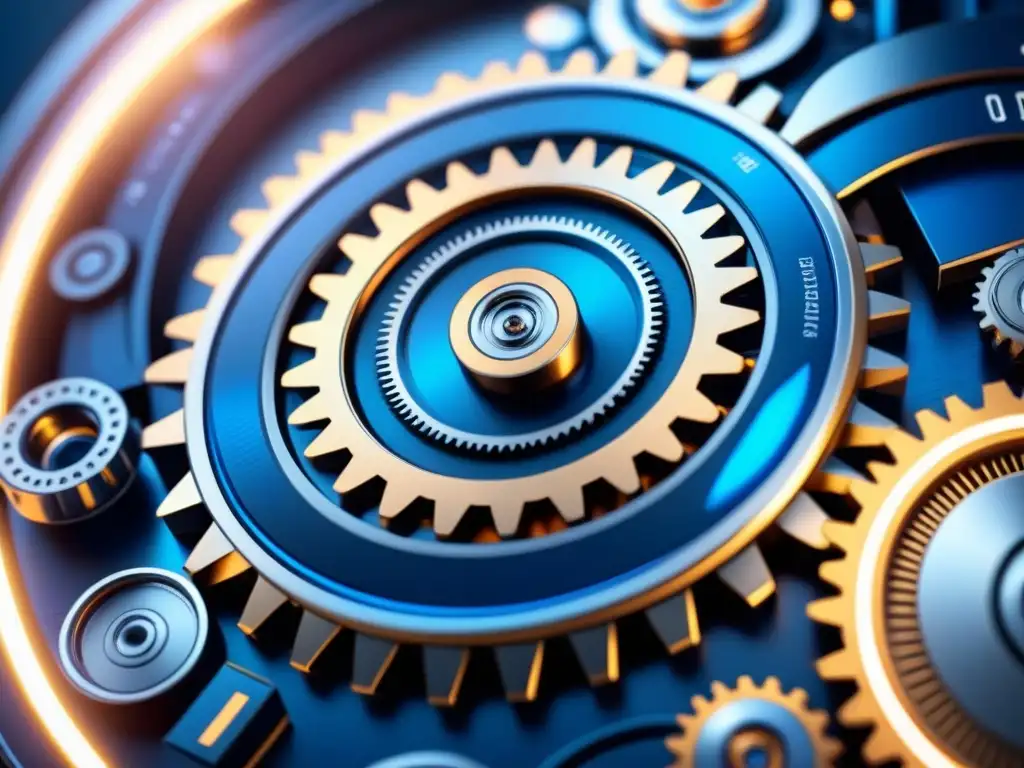
Resumen de beneficios y llamado a la acción para la industria
El análisis predictivo en mantenimiento se ha consolidado como un aliado fundamental en la industria actual, ofreciendo una serie de beneficios significativos para las empresas que lo implementan. Al aprovechar tecnologías avanzadas como el aprendizaje automático y el análisis de datos, las organizaciones pueden predecir y prevenir fallas en la maquinaria, reducir los tiempos de inactividad, optimizar los procesos de mantenimiento y prolongar la vida útil de los equipos.
Además, el análisis predictivo en mantenimiento no solo ayuda a evitar el desgaste y la obsolescencia de la maquinaria, sino que también contribuye a mejorar la eficiencia operativa, aumentar la productividad y reducir los costos asociados con reparaciones no planificadas. Esta herramienta proporciona a las empresas la capacidad de tomar decisiones informadas y proactivas en cuanto al mantenimiento de sus activos, lo que se traduce en un impacto positivo en la rentabilidad y la competitividad.
En este sentido, es fundamental que las empresas de diferentes industrias reconozcan la importancia del análisis predictivo en mantenimiento y consideren su implementación como una inversión estratégica a largo plazo. Aquellas organizaciones que aprovechan estas tecnologías emergentes estarán mejor posicionadas para enfrentar los desafíos del mercado actual y destacarse como líderes en sus respectivos sectores.
Preguntas frecuentes
1. ¿Qué es el análisis predictivo en mantenimiento de maquinaria?
El análisis predictivo en mantenimiento de maquinaria es una técnica que utiliza datos e inteligencia artificial para predecir posibles averías antes de que ocurran.
2. ¿Cuál es la importancia del análisis predictivo en la industria?
El análisis predictivo en la industria permite planificar intervenciones de mantenimiento de forma proactiva, evitando paradas no programadas y reduciendo costos.
3. ¿Cómo se implementa el análisis predictivo en el mantenimiento de maquinaria?
El análisis predictivo en el mantenimiento de maquinaria se lleva a cabo mediante la recopilación de datos, su procesamiento con algoritmos y la generación de alertas tempranas.
4. ¿Qué beneficios aporta el análisis predictivo en el mantenimiento industrial?
El análisis predictivo en el mantenimiento industrial optimiza la disponibilidad de la maquinaria, prolonga su vida útil y mejora la seguridad en las operaciones.
5. ¿Cuál es el rol de la tecnología en el análisis predictivo en mantenimiento?
La tecnología juega un papel fundamental en el análisis predictivo en mantenimiento al permitir la monitorización continua de los equipos y la generación de informes detallados.
Reflexión final: El poder del análisis predictivo en el mantenimiento de maquinaria
En un mundo donde la tecnología avanza a pasos agigantados, el análisis predictivo en el mantenimiento de maquinaria se erige como un pilar fundamental para prevenir el desgaste y la obsolescencia en las industrias actuales.
La capacidad de anticipar y prevenir fallos en la maquinaria no solo optimiza los procesos industriales, sino que también impacta directamente en la eficiencia y rentabilidad de las empresas. Como bien dijo Thomas H. Davenport, "La predicción no es solo un concepto valioso en sí mismo, sino que también es fundamental para la toma de decisiones efectivas". "La predicción no es solo un concepto valioso en sí mismo, sino que también es fundamental para la toma de decisiones efectivas" - Thomas H. Davenport.
Por tanto, te invito a reflexionar sobre la importancia de implementar el análisis predictivo en el mantenimiento de maquinaria, no solo como una herramienta tecnológica, sino como un aliado estratégico que puede marcar la diferencia en la competitividad y sostenibilidad de las empresas en el futuro.
¡Únete a nuestra comunidad e impulsa la innovación en la industria!
En nombre de Innovacion Industrial, queremos agradecerte por ser parte de nuestra comunidad y por tu interés en el análisis predictivo en mantenimiento como aliado contra el desgaste y la obsolescencia de maquinaria. Te invitamos a compartir este contenido en tus redes sociales y a explorar más artículos relacionados. ¿Qué temas te gustaría que abordáramos próximamente? ¡Esperamos tus comentarios!
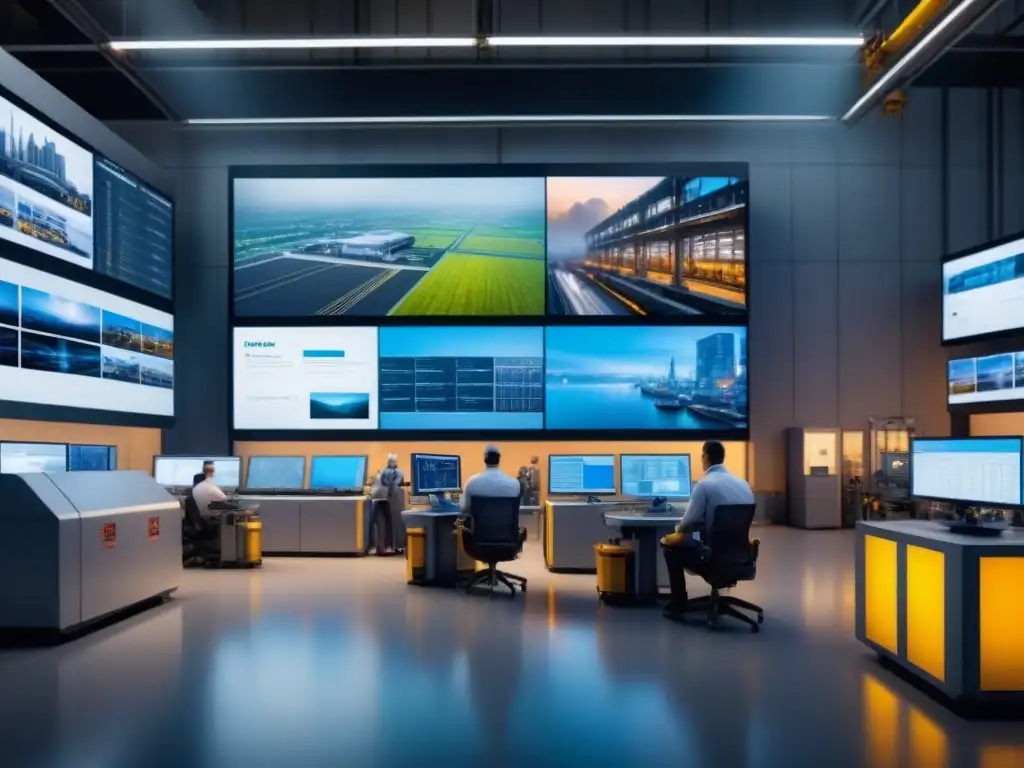
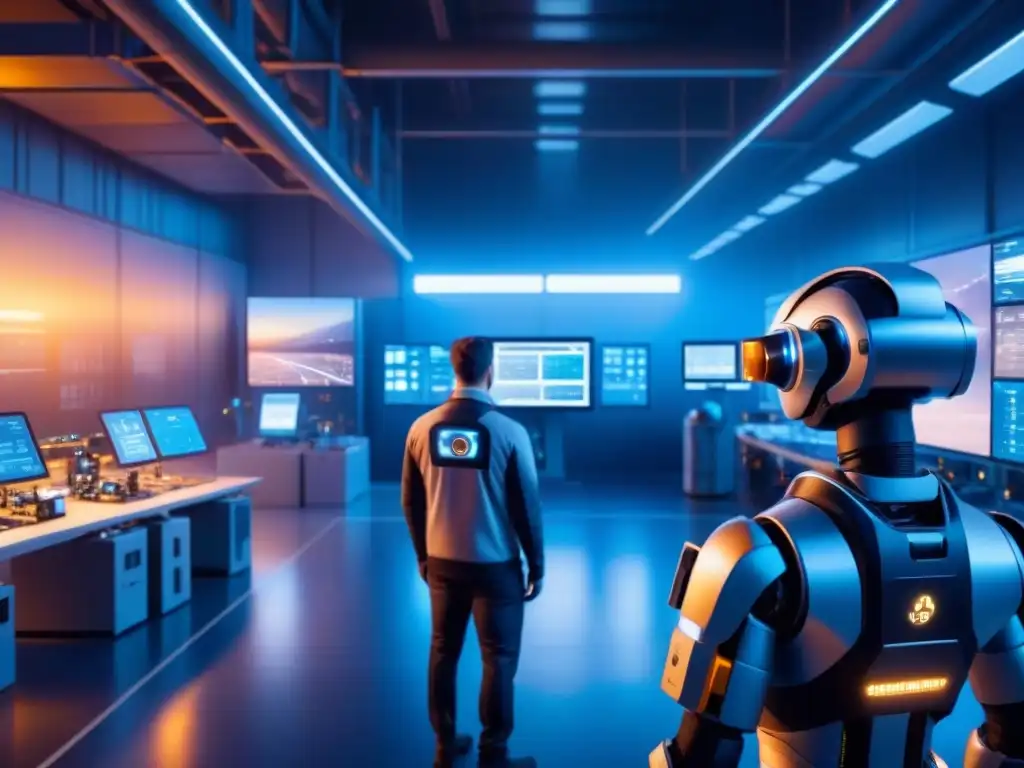
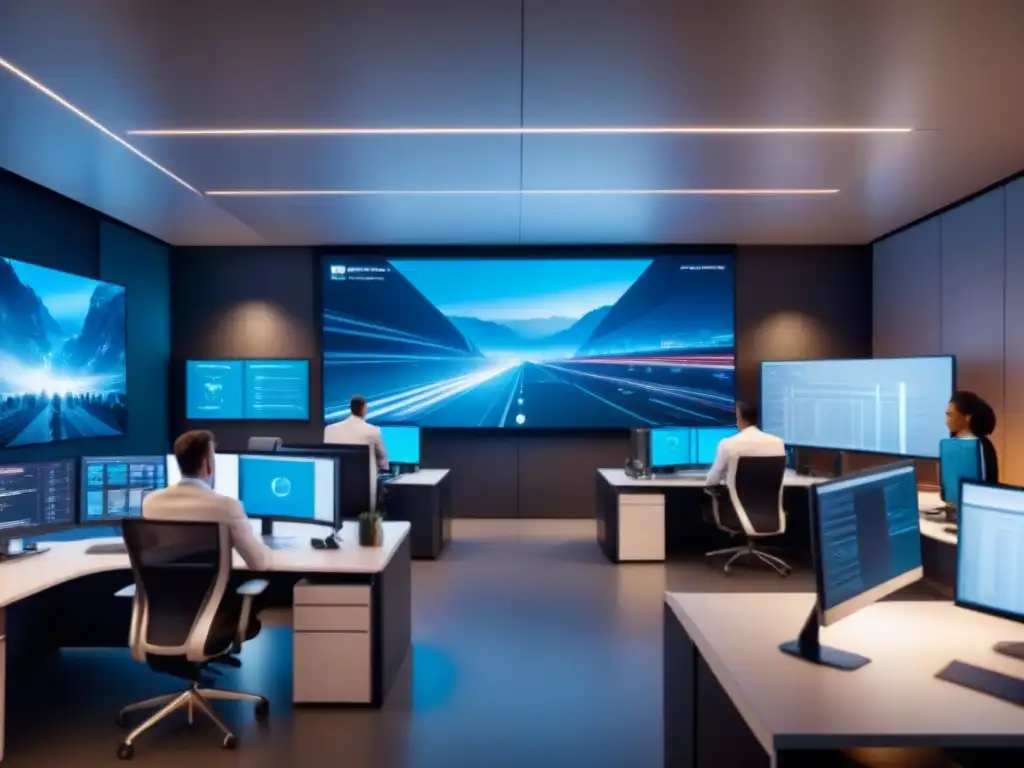
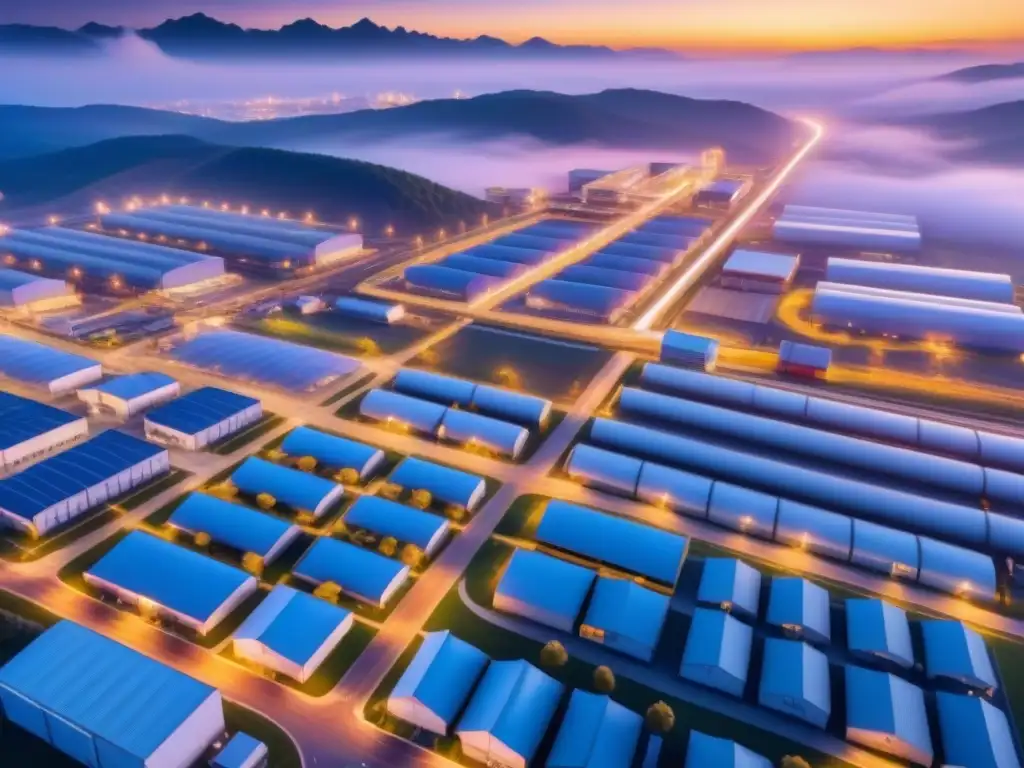
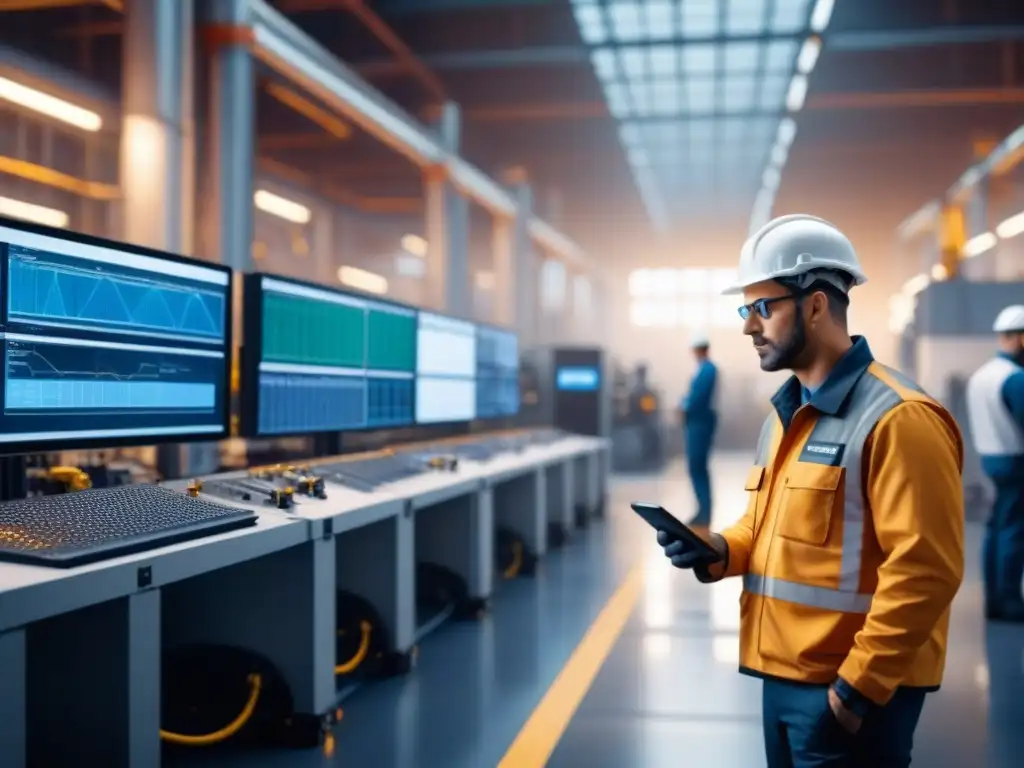
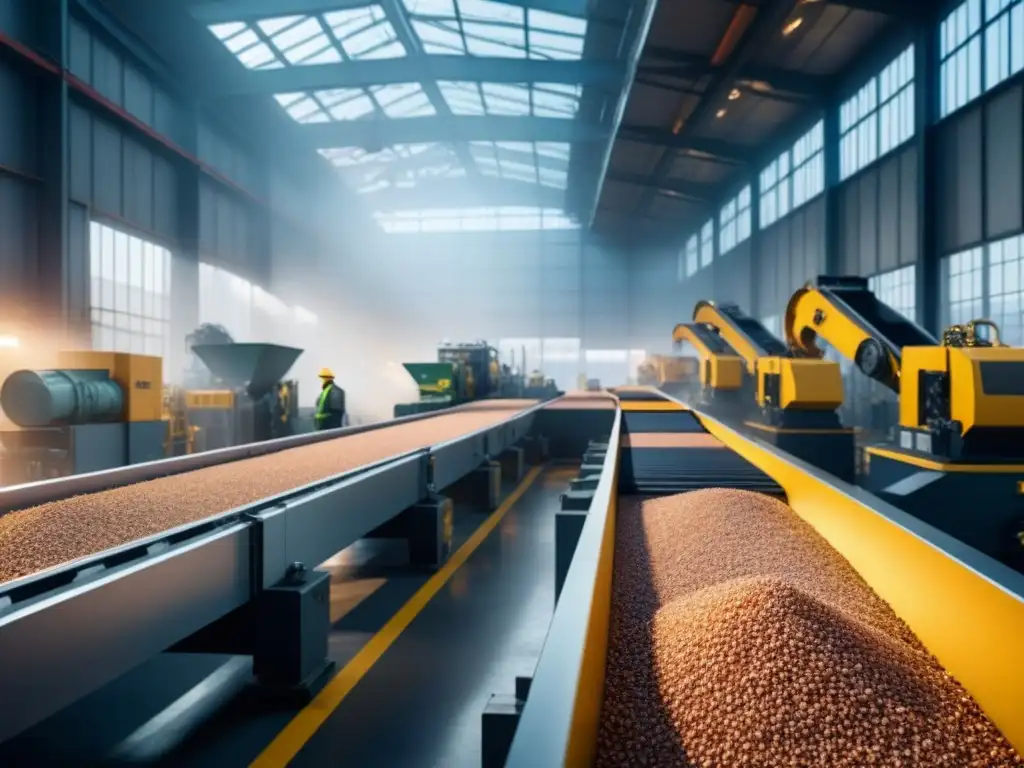
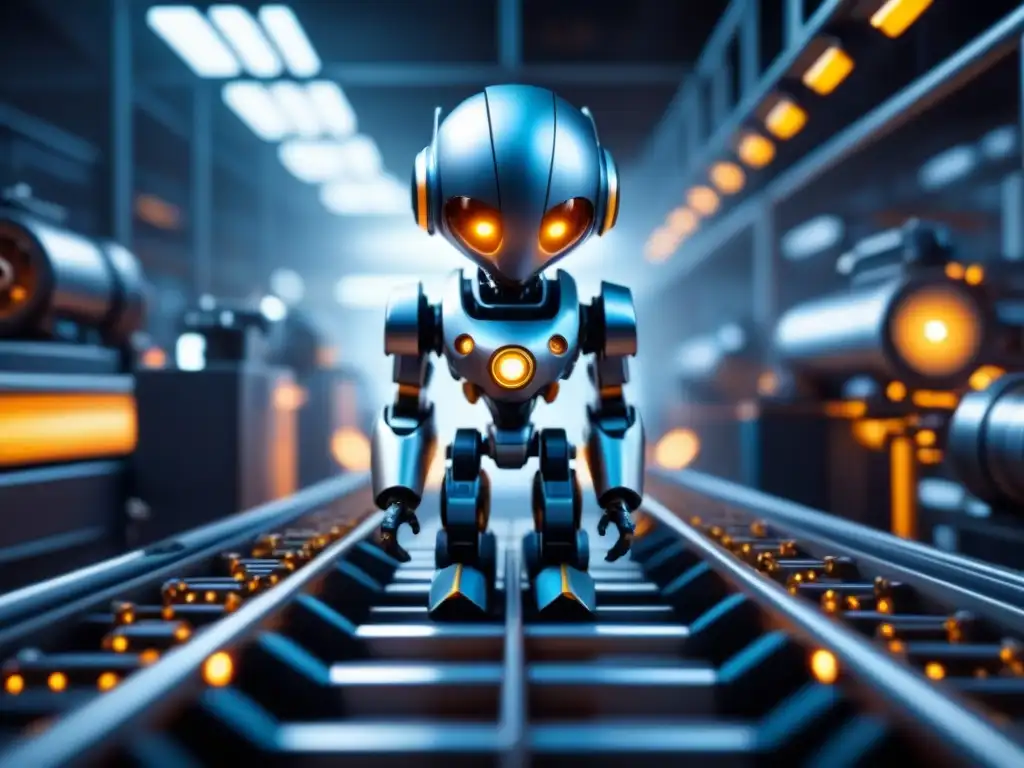
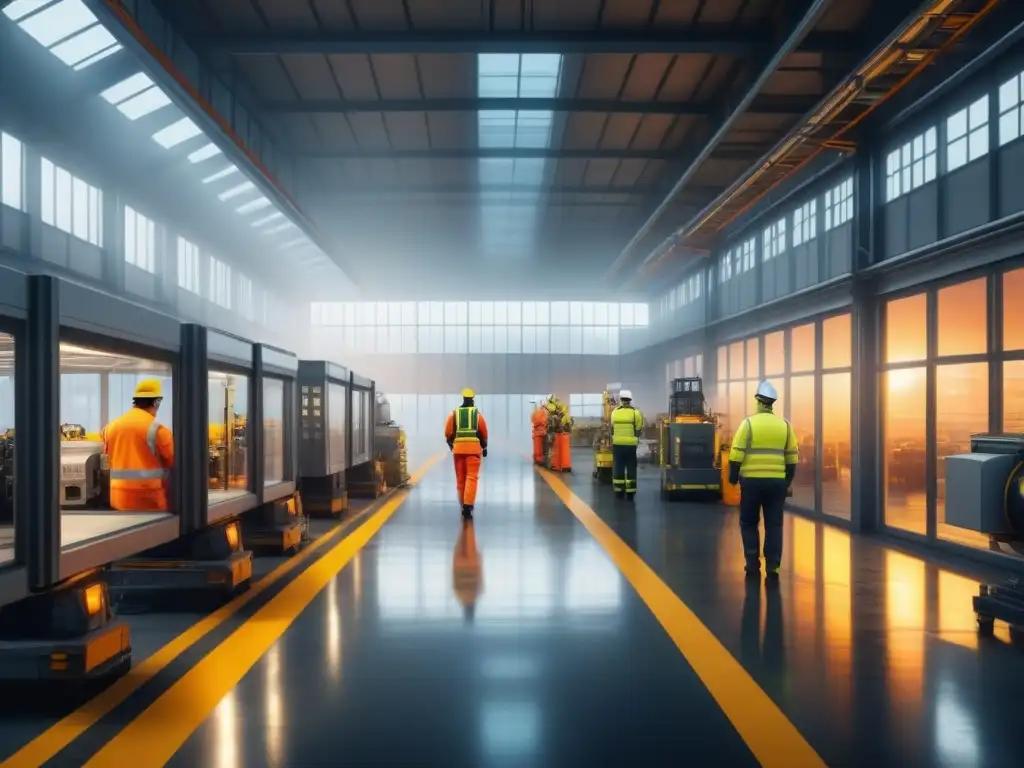
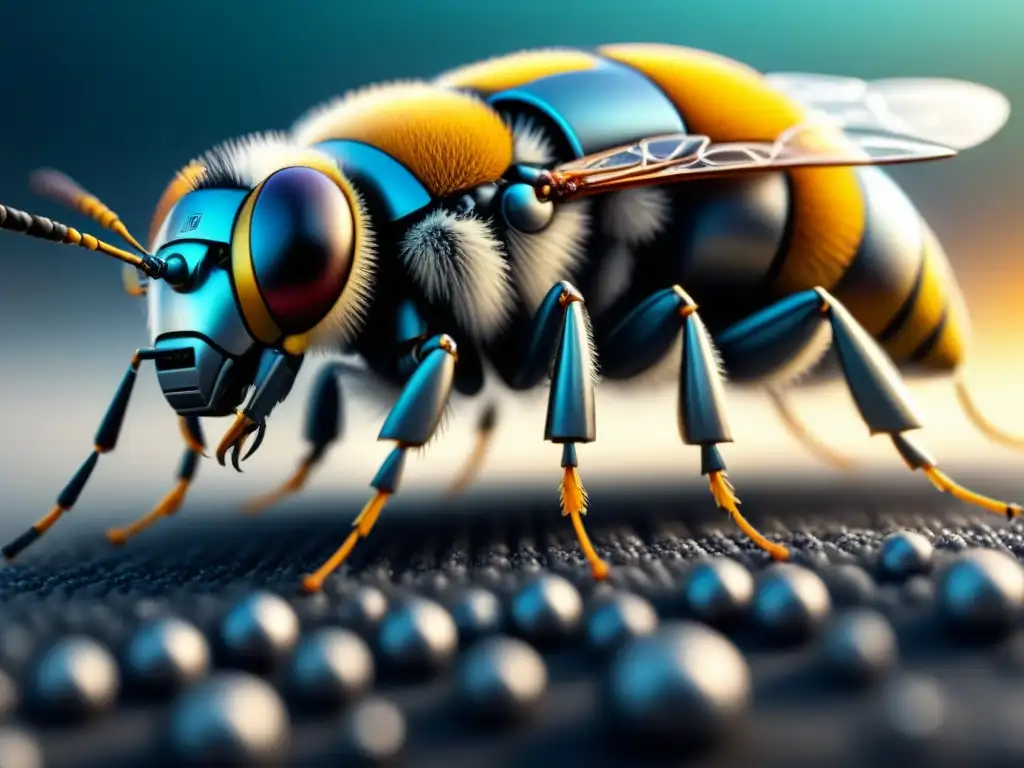
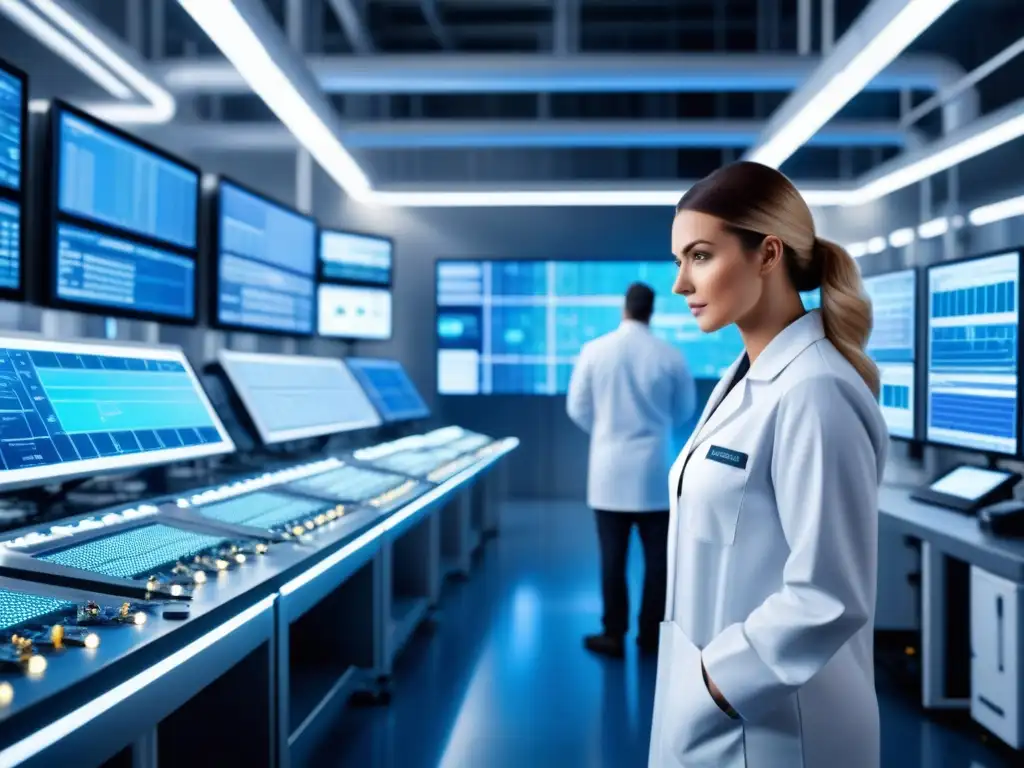
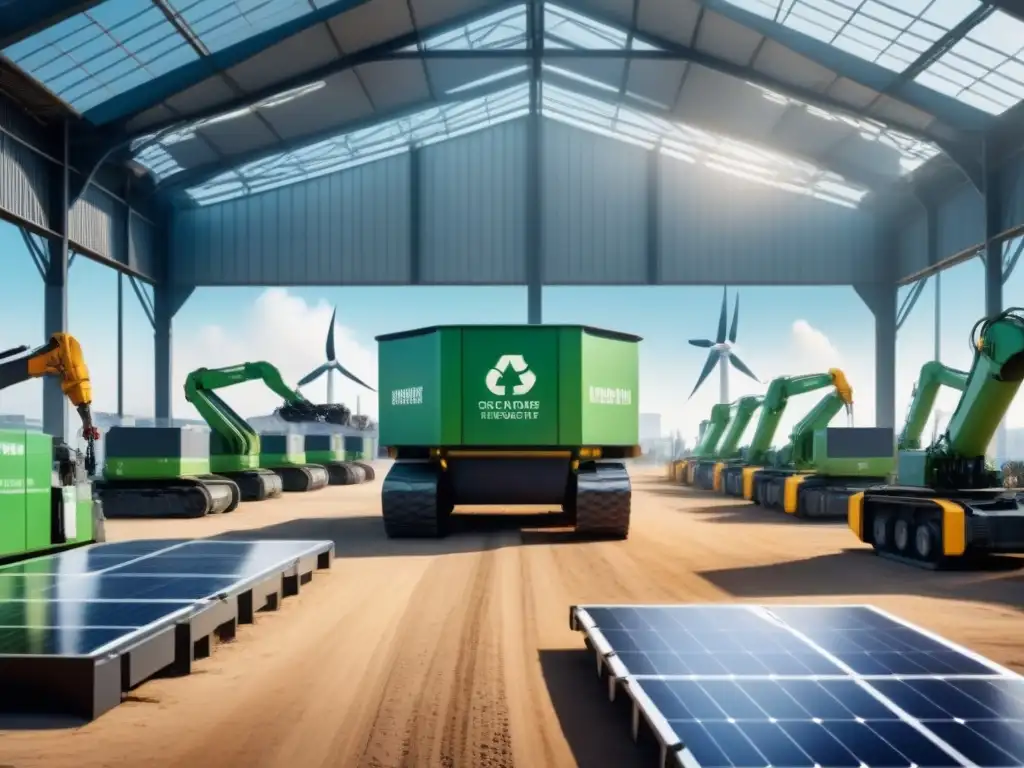
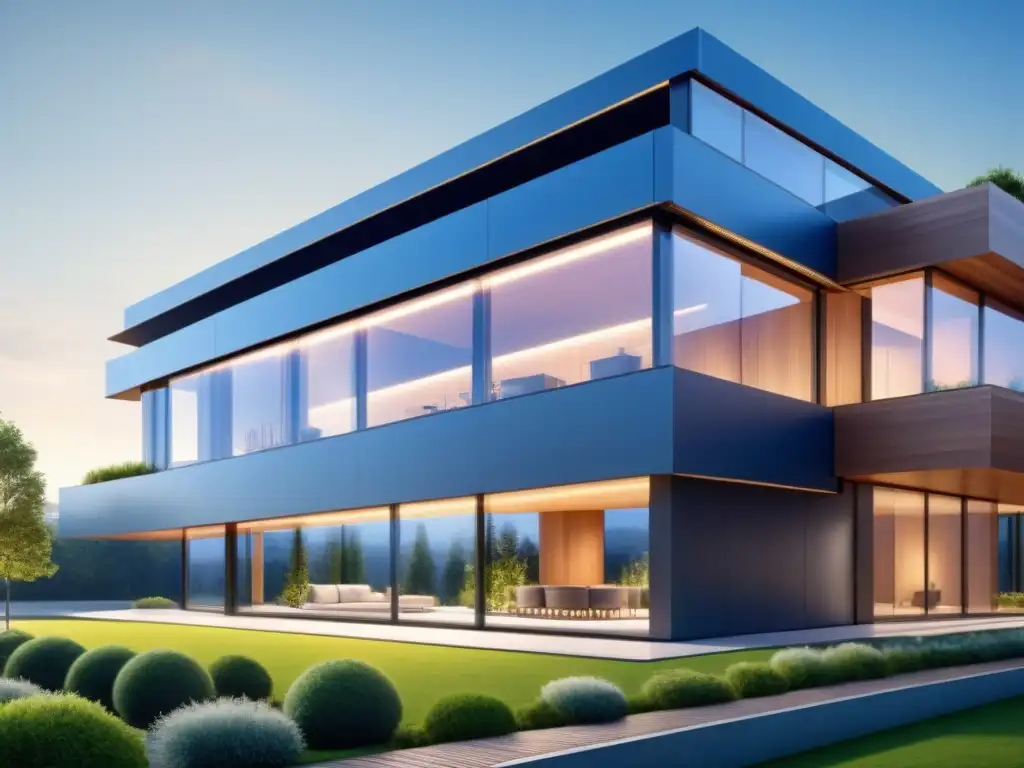
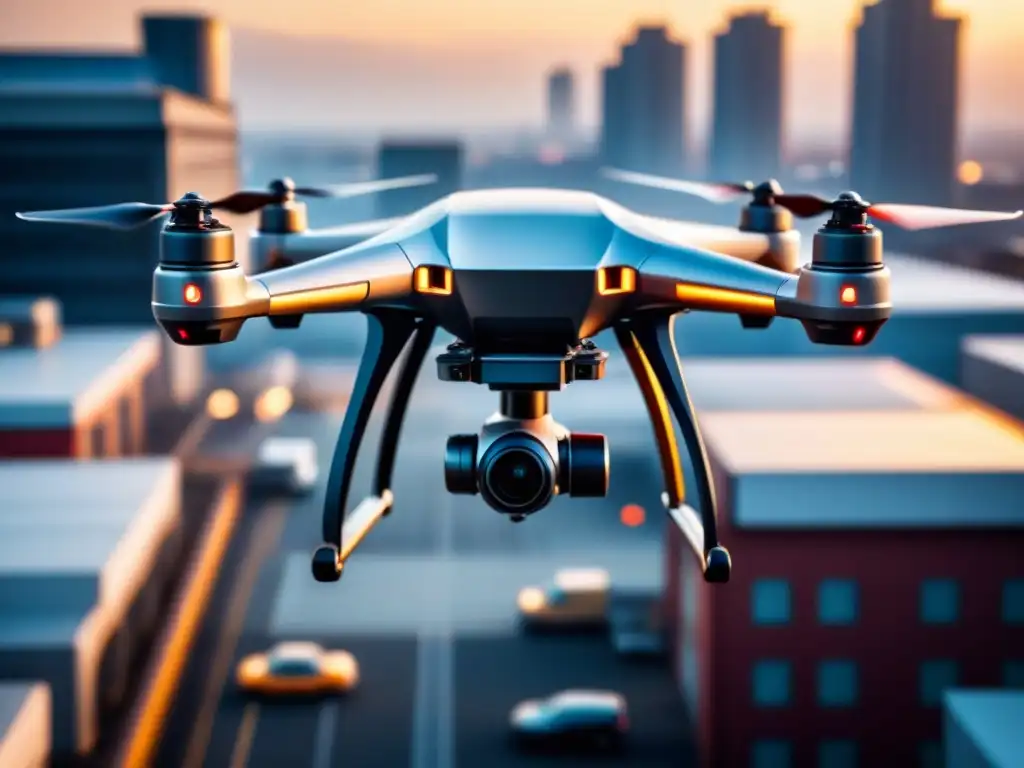
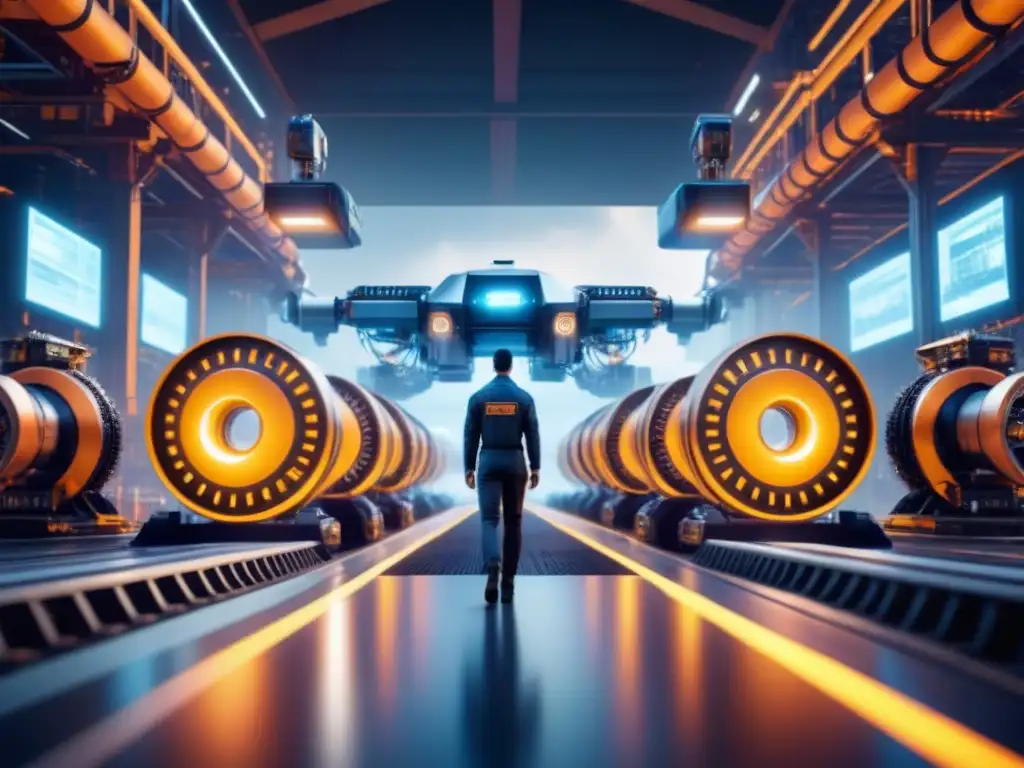
Si quieres conocer otros artículos parecidos a El análisis predictivo en mantenimiento: Un aliado contra el desgaste y la obsolescencia de maquinaria puedes visitar la categoría Análisis predictivo en mantenimiento.
Deja una respuesta
Articulos relacionados: